We have mentioned distributed electric propulsion in a few stories, but what is it for? It’s not about the motors. It is what is behind them!
There are different ways to approach a new technology like electrification. One way to go would be to simply replace like for like. So we could remove the conventional engine and fuel tank from a car, replacing them with a motor and batteries. This works, but is less than ideal, because the car’s designers already built it around that engine and fuel configuration.
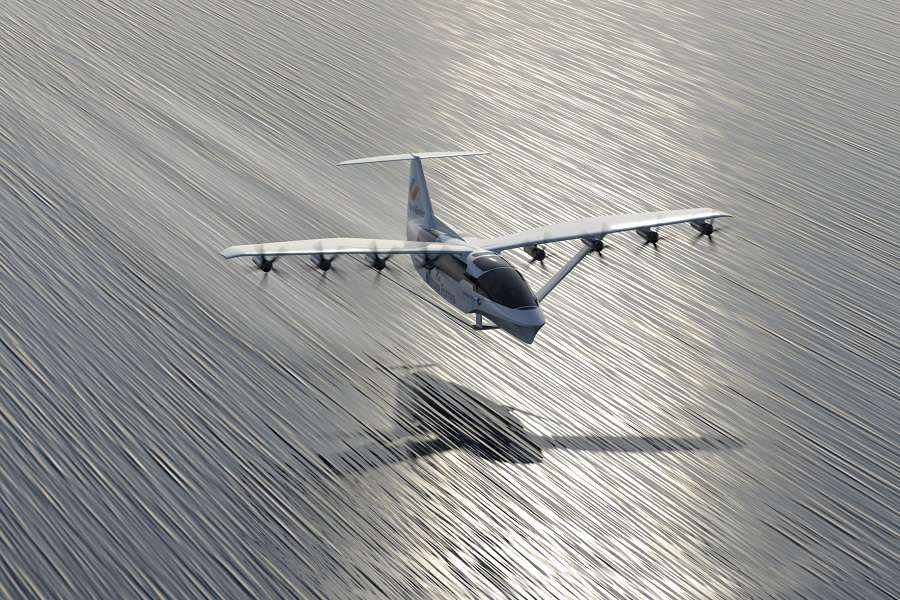
New technologies bring with them multiple design challenges. Distributed electric propulsion is about exploiting a potential advantage of electrification. While they’re trying to make electric flight a reality, engineers have to optimize its use with the airframe. In other words, engineers would use distributed electric propulsion, to get the plane to do something it couldn’t do before.
Firstly, we need to clarify that electric propulsion isn’t referring solely to all-electric aircraft. Hydrogen fuel-cell aircraft use electric motors for propulsion, too, distributed or not. Effectively, these craft are hybrid hydrogen-electric. The same goes for hybrid-electric vehicles that use an internal combustion or jet/turboprop engine, to create electric current.
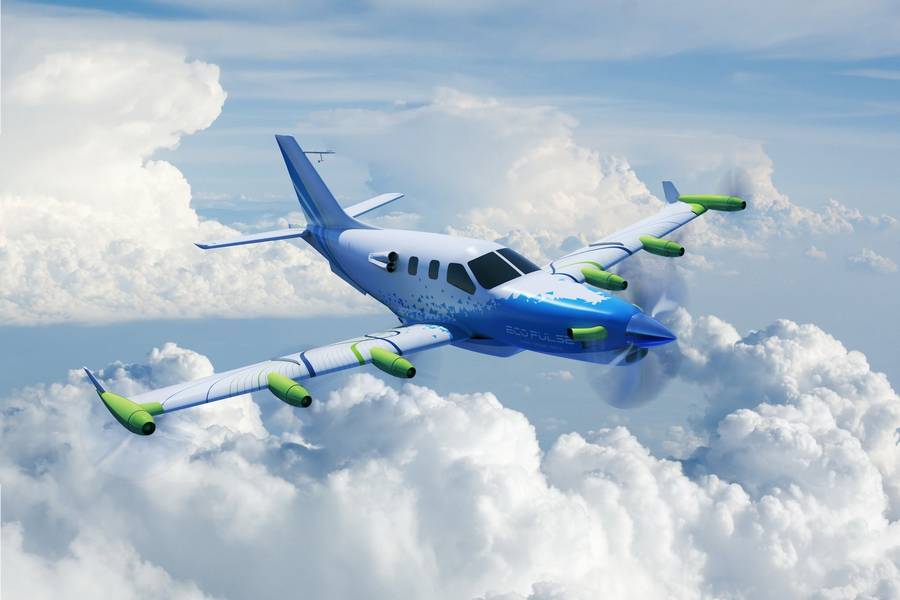
Distributed Electric Propulsion Changing Aerodynamics
With modern electronic flight control systems, aircraft manufacturers can use distributed electric propulsion in innovative ways. With other motors providing the most thrust, other, smaller motors can do other tasks. For example, with differential thrust, they can introduce roll and yaw moments. With the right programming, this technology could replace some movable aerodynamic surfaces! Or make them smaller.
We recently saw a joint project between Airbus, Safran and Daher, involving distributed electric propulsion. While Airbus isn’t working on a battery-electric concept at the moment, the technology has applications in its hydrogen plans. They will use the TBM’s original P&WC PT6A turboprop engine, combining it with a ‘turbogenerator’, to drive the electric motors. The proof-of-concept project should stand ground testing in 2022.
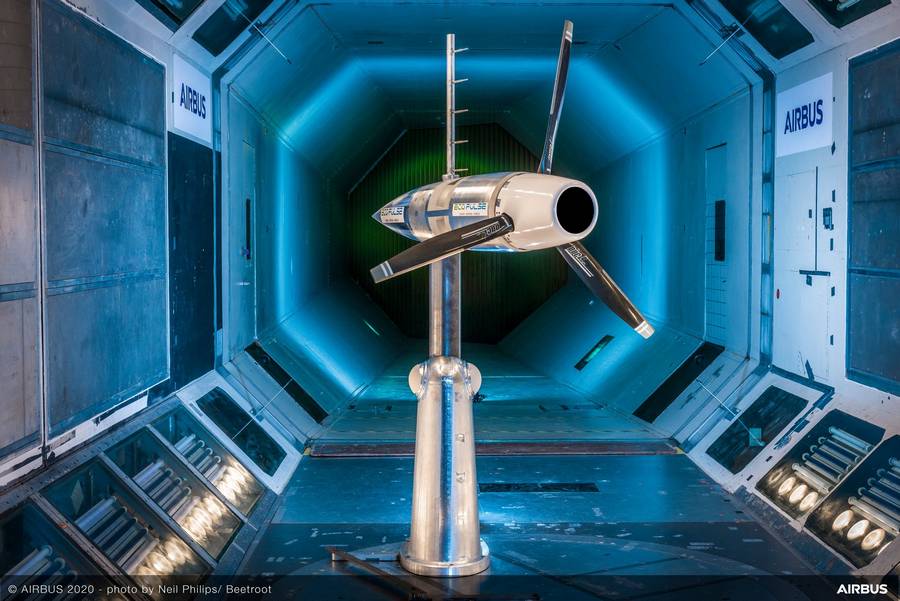
But NASA has a more ambitious distributed electric propulsion project, that they call the X-57. This aircraft uses the fuselage of a Tecnam P2006T. This high-wing aircraft normally has a pair of 100hp Rotax 912 engines on its wings. And these wings are a… normal design, compromising between good cruise speed and acceptable low-speed performance for takeoff/landing.
All About Wing Efficiency
NASA doesn’t intend to limit or reduce the number of movable aerodynamic surfaces in its distributed electric propulsion project. In its definitive form, the X-57 will feature a high aspect-ratio wing. This wing has a much smaller surface area, so it also has a much higher wing loading. This will make the aircraft much more efficient in cruise. However, this would normally increase its takeoff and approach speeds considerably.
That’s where distributed electric propulsion comes in. NASA’s X-57 will have twelve small electric motors, i.e. six on each wing. These are on top of the two main ‘cruise’ motors. Those bigger motors will be on the wingtips, further reducing drag by negating wingtip vortices. The company supplying these bigger motors is Joby Aviation, whose urban air mobility project we saw recently.
Joby Aviation worked with NASA on the first phase of the X-57 project. This involved ground testing a wing, complete with electric motors and propellers. It’s an unusual look (below) for a test vehicle, for sure! But NASA will use different propellers for the distributed electric propulsion motors on the wing. Their design and hub allows them to fold backwards, when not in use. This should eliminate most of the drag in cruise.
Getting To Distributed Electric Propulsion – Slowly
NASA’s X-57 will first fly with the standard wing, and the two big motors in place of the normal engines. They have already been performing ground tests with the vehicle in this configuration (see below). But the next step will be to fly the plane with the new, high aspect-ratio wing and the same two motors. In the last step, the aircraft will fly in its final form, with 2+12 motors.
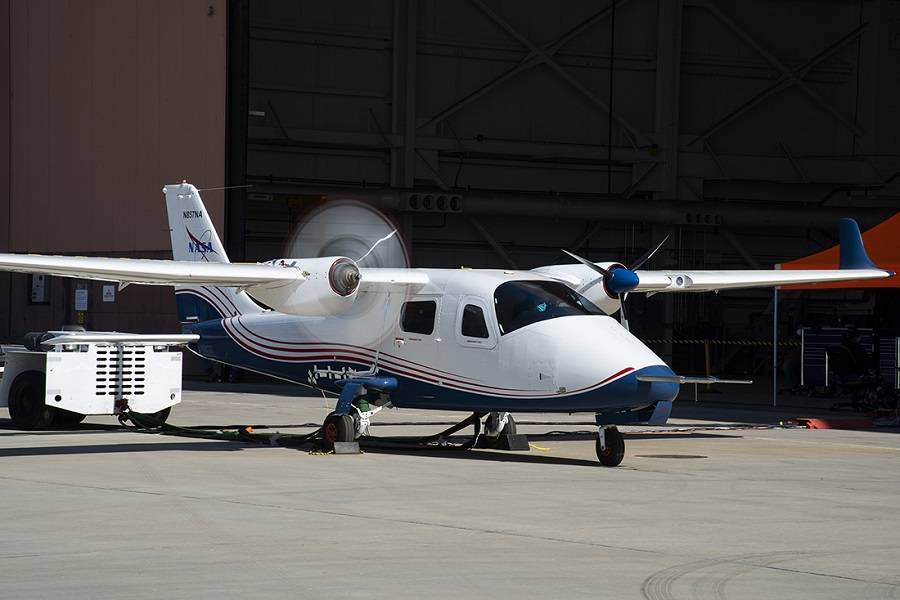
What NASA is hoping to prove, is that with all motors running, the X-57 will take off and land at the same speeds as a normal Tecnam P2006T. But it should be more efficient in cruise, requiring less power for the same speed. So the distributed electric propulsion layout should, in itself, improve the aircraft’s efficiency.
Along the way, NASA is also busy testing every other aspect of flying an all-electric aircraft. And this includes testing lithium-ion batteries, to limit and/or contain thermal runaways. This is a challenge for all current battery-electric aircraft designs. And just as importantly, there is the design of a control and power distribution system. Distributed electric propulsion adds a fair amount of complexity, by default.
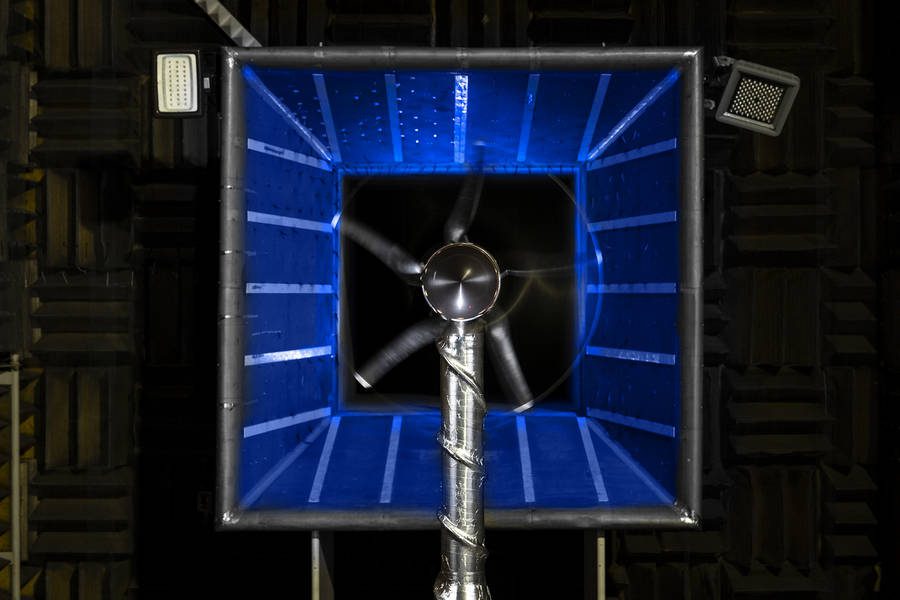
NASA’s research should benefit a multitude of eVTOL and other urban air mobility designs. Some of these projects seem to be underway without all the elements into place. So NASA is taking on the same innovation-promoting role in these projects, as it has in the rest of aviation!