Airbus and its partners in the EcoPulse hybrid project, announced the completion of wind-tunnel testing of its distributed propulsion system.
The project passed the preliminary design review stage last December. The next step was to test the new distributed propulsion system in the Airbus wind-tunnel, in the UK. More wind-tunnel testing will come later, with the motor, propeller and cowling assembly on the aircraft’s wing. But this initial test of the components themselves is key, because they are the actual parts, in 1:1 scale.
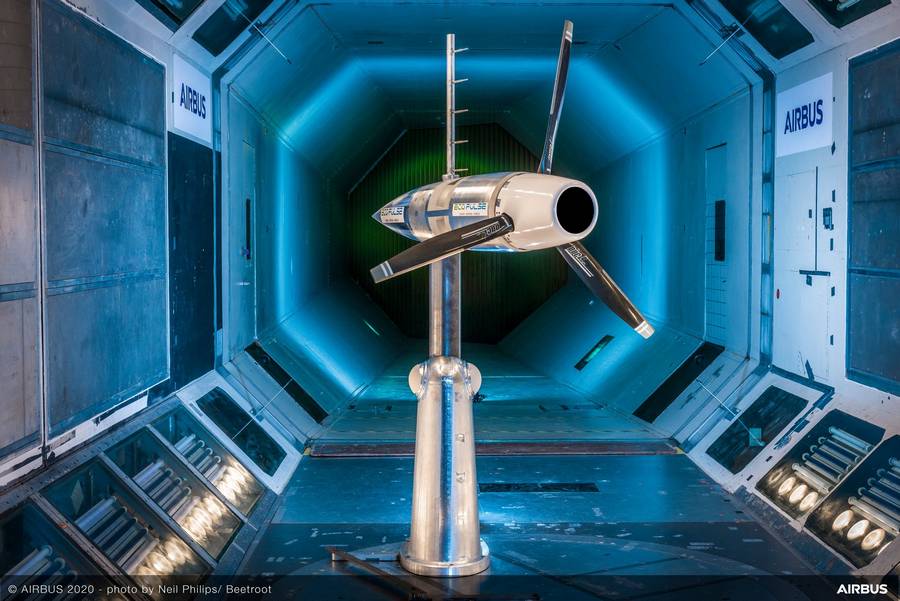
Airbus, Daher and Safran announced the EcoPulse program at the 2019 Paris Airshow. It has support from the French Civil Aviation Research Council (CORAC) and the French Civil Aviation Authority (DGAC). Also, DUC Hélices is supplying the propellers for the project. The EcoPulse demonstrator will use the airframe of a Daher TBM 900.
The idea behind the distributed propulsion system is to make more efficient use of the aircraft’s turboprop engine. Airbus and its partners will use a ‘turbogenerator’, to power multiple electric motors on the wings of the EcoPulse demonstrator. In addition to any sustainability benefits, the layout can also offer improved take-off and landing performance.
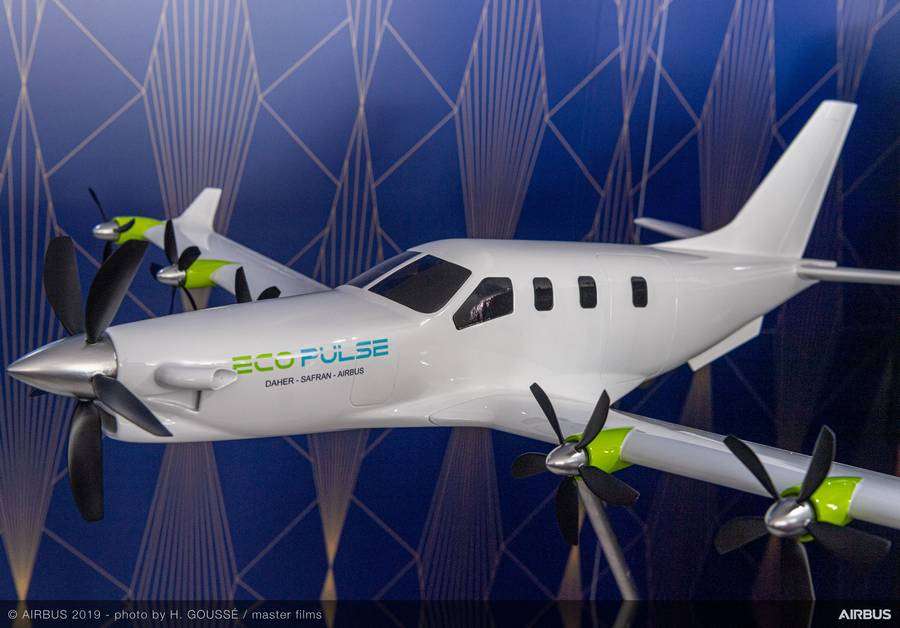
This improved performance will come from the accelerated airflow over the wing. Noise emissions should also be lower, when the aircraft is near airports. Also, the presence of so many propellers over the wings could have some other interesting implications. Airbus wants to use the EcoPulse demonstrator to explore some alternative flight control concepts.
State Of EcoPulse And Airbus Goals
Airbus’ wind-tunnel testing of the EcoPulse propulsion system had two main goals. Firstly, it needed to evaluate the performance of the DUC propeller. This also includes the shape of the wake the propeller creates, which will affect how it interacts with the wing. Secondly, the test needed to validate the cooling system within the electric motor. The Airbus-made nacelle is a key part of the assembly in this regard.
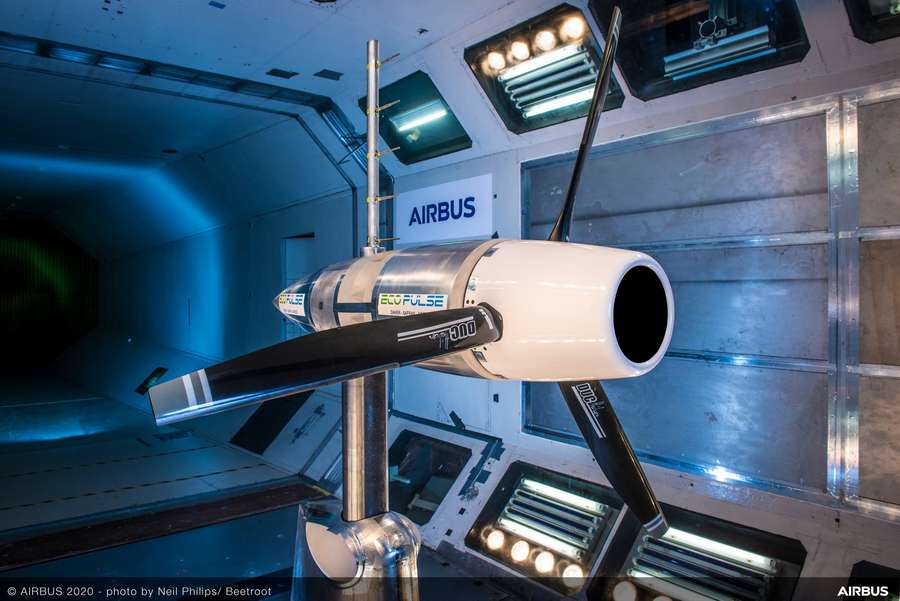
Airbus gradually abandoned plans for all-electric aircraft – but the EcoPulse is hybrid-electric. With their focus on hydrogen, Airbus needs development work on electric propulsion, that this project should offer. And with some hydrogen aircraft concepts having as many as six engines on the wing, the distributed propulsion data will have its value.
One partner of Airbus in the EcoPulse project is Safran. We know the company as one of the partners in CFM, the makers of jet engines powering many single-aisle Airbus and Boeings. Safran is making the 50 kW electric motors. These ENGINeUS motors come with integrated electronics and air cooling, the latter being part of this wind-tunnel testing.
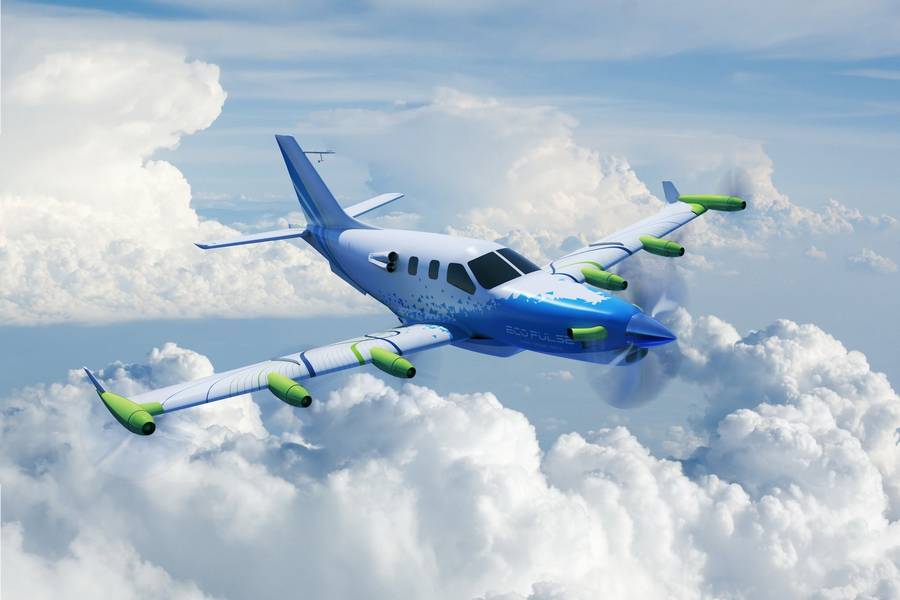
The motors will need EASA certification, like any turbine, turboshaft or internal combustion engine. Safran has already made and certified other electric motors. Also, the company makes the turbogenerator and relevant high-voltage wiring. However, we don’t know how Safran integrate this turbogenerator to the TBM’s PT6A engine. The maker of this engine is Pratt & Whitney Canada.
Daher (formerly SOCATA) should start building the demonstrator aircraft in the coming months. This will come after Airbus, Daher and Safran jointly conclude the EcoPulse’s Critical Design Review (CDR). And if all goes according to plan, the demonstrator should start ground testing in 2022.