Airbus is establishing two development centres on existing sites, for cryogenic hydrogen fuel tanks. And it’s a major challenge, to say the least.
Starting from last September, Airbus started a programme that will lead to a future fleet of hydrogen-powered aircraft. At the time, they explained that they will be looking at multiple types of hydrogen propulsion. This would include hydrogen combustion and fuel cells. Separately, Airbus also said that they would look into both pressurized and liquefied, cryogenic hydrogen. Their goal was to have the first hydrogen-powered aircraft in service by 2035.
We recently saw that the manufacturer moved to clarify (or play down) this timeline, somewhat. The introduction of that first aircraft doesn’t mean that a rapid succession of other hydrogen designs will follow. They expect widespread usage of hydrogen to take another 15 years beyond 2035. Of course given how airlines replace their fleets, this isn’t surprising.
Separately, there are significant challenges in creating the necessary supply chain for the fuel, and its handling at airports. Airbus launched projects for the handling of both pressurized and cryogenic hydrogen in this regard. But when it comes to aircraft, Airbus now seems to have decided on cryogenic hydrogen. And one of the biggest challenges in making it work, is the fuel tanks it will be in.
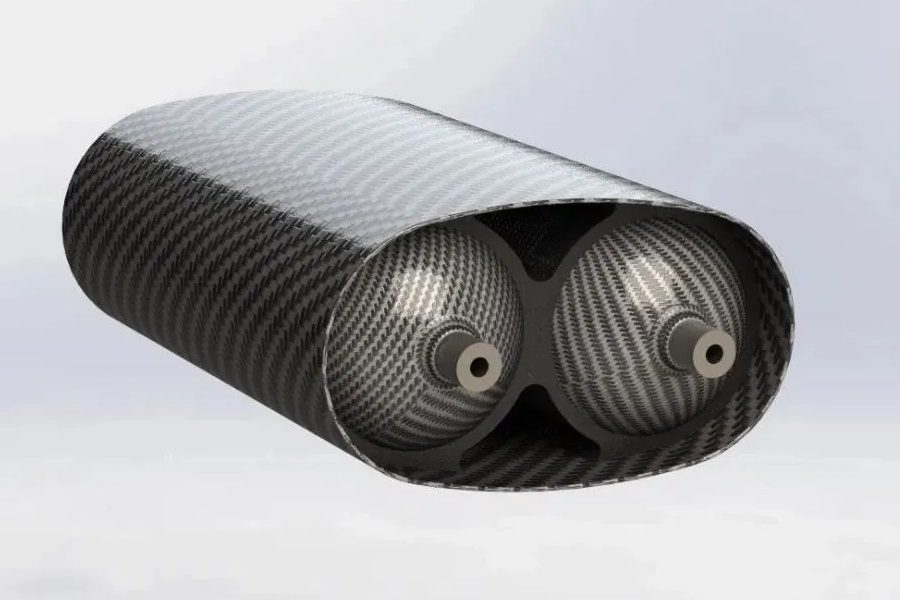
Existing Uses And Benefits
Cryogenic hydrogen isn’t a new fuel. A lot of space launches have used and are using it, as their rocket fuel. The Space Shuttle was one of them. But the tanks in these applications typically are single-use. Obviously, to use them in aircraft, the challenges are quite different. Other hydrogen applications, e.g. with very small aircraft, often use pressurized hydrogen. But Airbus needs the extra density that cryogenic hydrogen brings.
For hydrogen to become a liquid, its tanks need to keep it at extremely low temperatures: -250°C (-418F°). That’s 23 Kelvin! This poses extreme demands on fuel tanks. It also causes a lot of hassle in handling the material, and it the necessary infrastructure for it. The benefit? Density. These temperatures would allow aircraft to carry much more fuel than pressurized tanks.
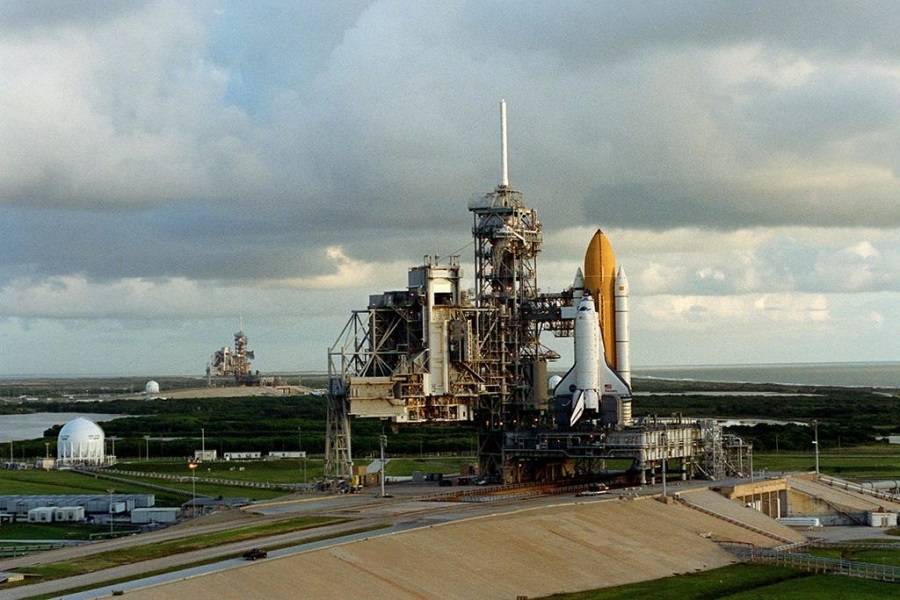
But unlike a space launch vehicle, an aircraft goes through multiple cycles, in both pressure and temperature. This is a challenge on a different level, that Airbus will have to solve for cryogenic hydrogen to work on its aircraft. And it is one reason why they are sticking to metallic LH2 tanks, at least to start with.
Cryogenic Hydrogen And Airbus
Fortunately for Airbus, they have a department that has used cryogenic hydrogen for years. Airbus Defence and Space includes ArianeGroup, the company managing ESA’s Ariane launch vehicles. Their current such vehicle is Ariane 5, the first and second stages of which use liquid hydrogen and oxygen. So, Airbus chose its site in Bremen, Germany, for the development of cryogenic hydrogen fuel tanks. This site has been behind the handling of these fuels for launch vehicles, for decades.
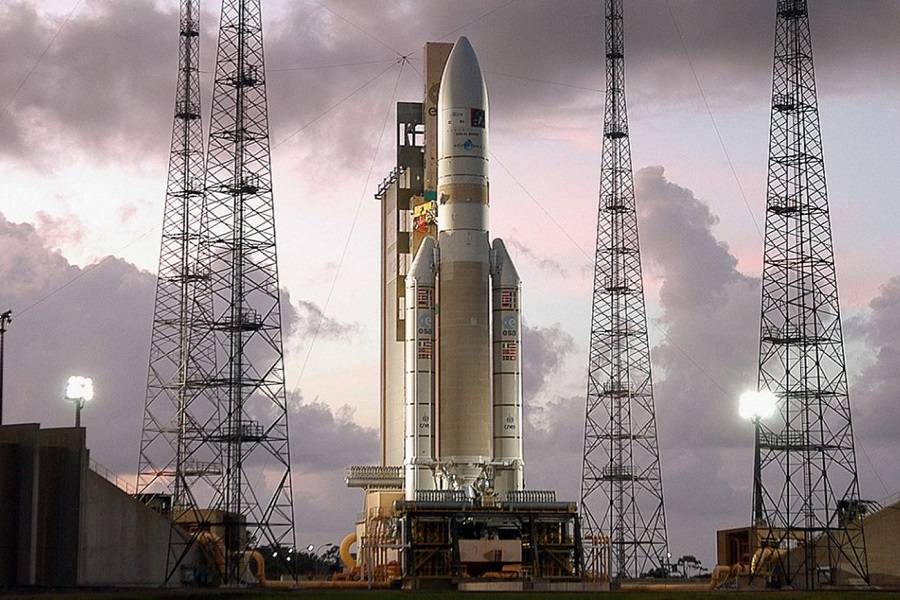
Airbus is creating two Zero-Emission Development Centres (ZEDCs) for this project. One is in Bremen, the other in Nantes, France. The latter site has extensive knowledge in critical aircraft structures, including structural fuel tanks. We recently saw their work on developing the A321XLR’s Centre Wing Box (CWB) and the new Rear Centre Tank (RCT). Airbus aims for the two ZEDC sites to work together on metallic cryogenic hydrogen tanks and related technologies.
Ultimately, Airbus hopes that it will be able to develop cryogenic hydrogen tanks using composites. These could offer substantial weight benefits – when they come. But with a big-enough challenge in liquefied hydrogen, it seems that Airbus decided to start with what it knows best. However, there is still some way to go, for all this to come to fruition.
Also, it will be interesting to see if Airbus will share technologies on cryogenic hydrogen storage. Airport handling of hydrogen could benefit from developments in this area, as well. And of course Boeing, too, have experience with hydrogen in launch vehicles – and decided against it, in aircraft. So there could be more to come from this story!
1 comment
Andre T
Having worked on rockets with design experience with hydrogen vents and commercial turbine fan engines, I’m highly sceptical. First, engineering for rockets versus aircraft is different. Engineers working rockets are likely not going to have experience of high cycling durability of commercial aircraft especially with the engines. Likewise engineers on aircraft side are likely not going to have experience with cryogenic fluid systems. Unless AB has a number of engineers that worked both sides, they are not going to have the appreciation of the real challenges. Boeing may have this experience and knows the challenges. Hence why they shy away from it.
The hydrogen tanks are probably the less challenging part of the hydrogen system. But none the less challenging. Can they withstand aircraft crashes and what happens if a hydrogen tank ruptures? How about what happens when hydrogen fuel lines crack? It will happen. It happens all the time on commercial engine vast majority don’t result in fire with jetA fuel. Cryogenic hydrogen is going to put even more thermal cycling stresses resulting in cracking.
I just don’t believe the safety of cryogenic hydrogen has been demonstrated in high cycle aircraft. In my option crash tests need to be done. I also don’t believe cryogenic hydrogen is practical for high cycle aircraft operations. SAF is the better path in many ways.