Supply problems have hit Boeing and others before but didn’t stop the production of the 737 or other aircraft completely. So what changed?
Boeing has had production issues before, most recently with the 787. While those were technically delivery problems, not production problems, they certainly had to do with faults of some sort. Boeing is currently in talks with the FAA to finalize the ways it will inspect its backlog of 787s.
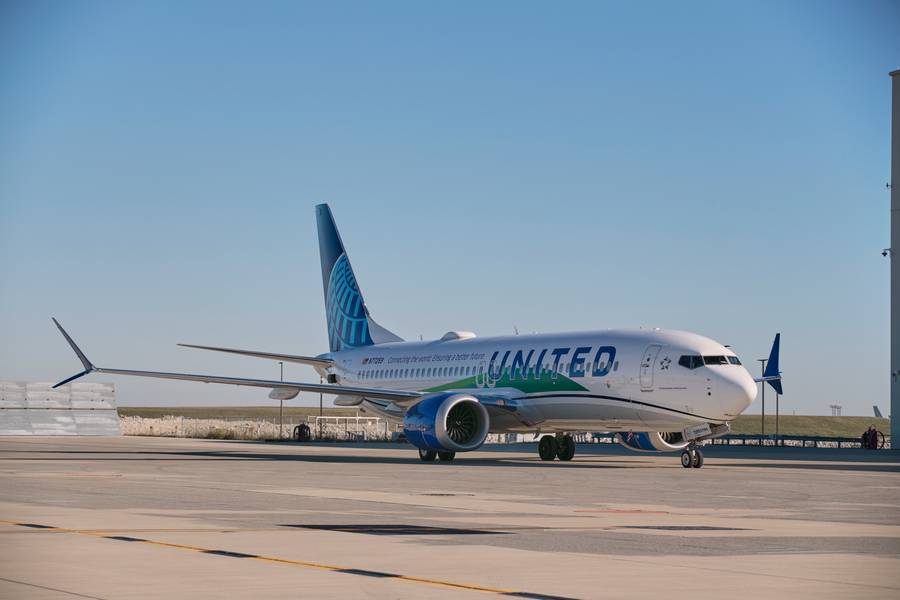
Boeing stopped production of the 737 MAX when the type was grounded. But the aircraft returned to service over a year and a half ago now. Boeing is busy working on the certification of the remaining variants of the family. But this production stoppage affected current variants of the aircraft. According to several sources, the problem has to do with a wiring connector.
All components for certified aircraft come with appropriate certifications and approvals. So Boeing can’t simply substitute a “lowly” wiring connector with a different part to continue 737 production. The pandemic has caused many supply chain disruptions around the world, including some for seemingly “simple” components or raw materials. Sudden, mostly unpredictable lockdowns and/or additional controls had this effect, among others.
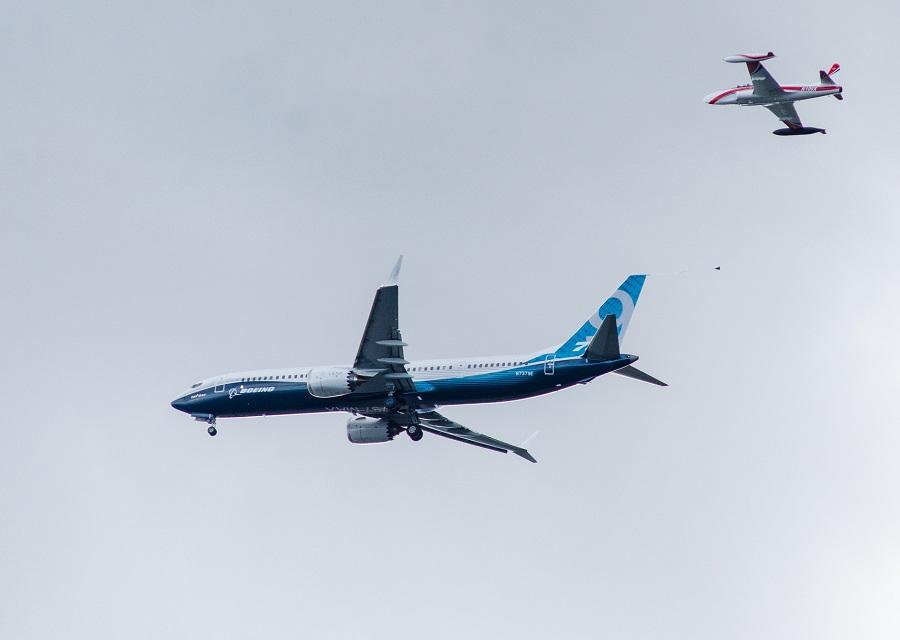
Keeping Things In Stock
One aspect of serial production that likely has a role in Boeing’s 737 issues in May is “Just in Time” manufacturing. In simple terms, this is a process that allows a manufacturer to avoid having to keep large stocks of any one part in storage. The principle applies to complex machines like cars or aircraft. With thousands or even millions of parts, the storage space and sorting facilities that large stocks would demand, pose limits to production.
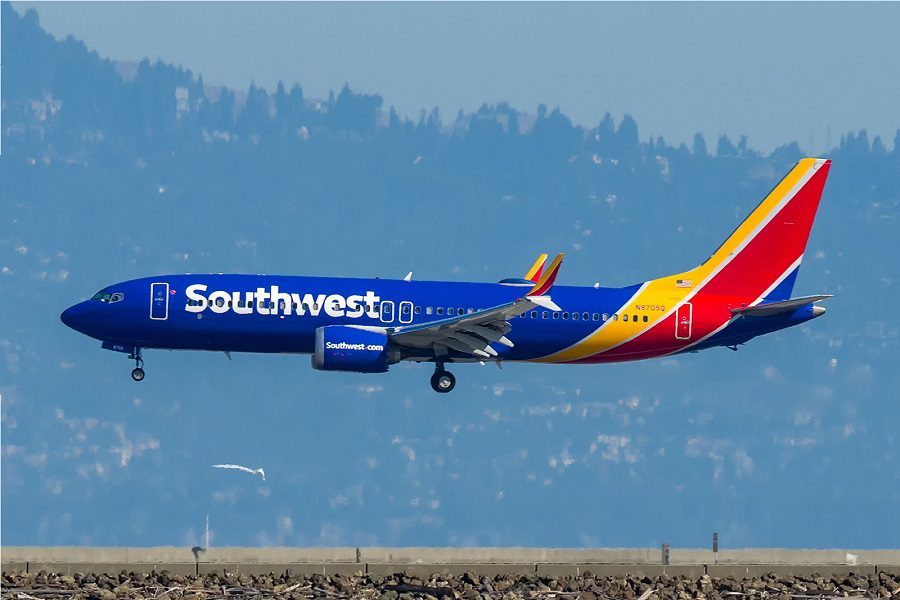
As its name suggests, “Just in Time” manufacturing has the necessary parts entering the factory just when they are fitted on the product. But as Leeham News explains, this requires quite an advanced level of coordination and timing, with suppliers and contractors having their own sub-contractors, with their own supply chains. And in the pandemic, this long-established choreography faltered – or failed.
To keep its 737 production going, Boeing had to introduce some stocks of key parts. Other manufacturers and first-tier suppliers did the same thing. But this is far from the whole story. The pandemic and its aftermath may have been (and in places, still are) a challenge. But this is not the first time that Boeing has had delivery delays for key components.
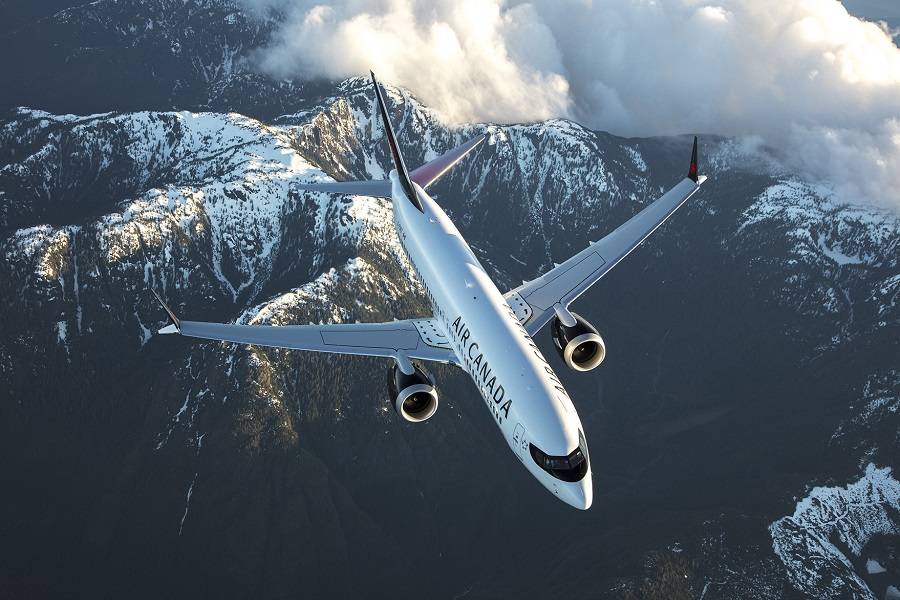
737 Production And “Travelled” Work
Airbus has had to contend with similar issues in the past, as well. And when they did, the manufacturers did not have to stop their 737, A320 or other production lines, for 10 days or more. What they did, was to keep the production line moving, and worry about any missing parts later. Obviously, this doesn’t work for ALL parts. But it is often possible to continue the rest of the assembly, without stopping production.
This is called “travelled work” and can be a necessary evil of just-in-time manufacturing. But it is something manufacturers try to avoid as much as possible. It is often necessary to disassemble multiple components to reach the location of missing parts. This makes such work labour-intensive and inefficient. It can also introduce failure points and quality issues.
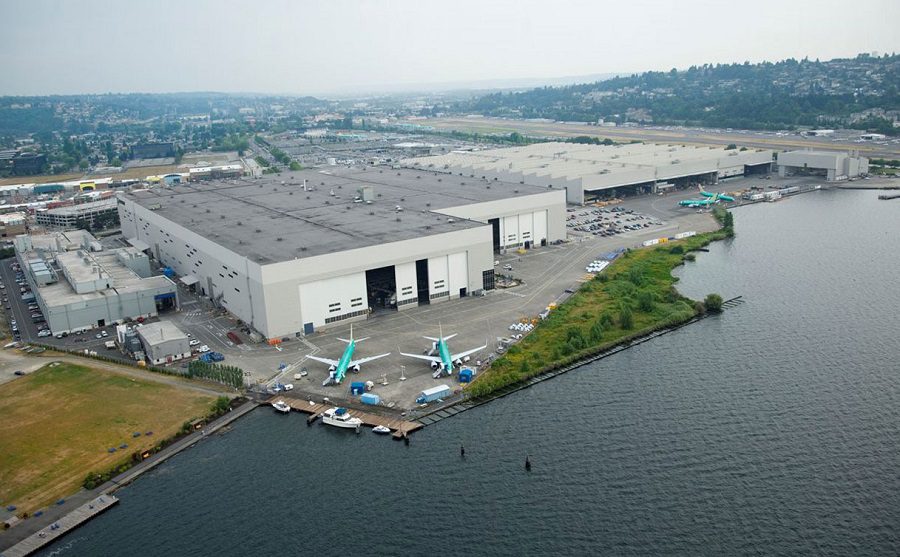
So in May, Boeing decided to stop its 737 production line in Renton, keeping the aircraft in the line, rather than taking them outside and “travelling the work”. Boeing is still lagging behind Airbus considerably. The American manufacturer targets a production rate of 31 737 MAX aircraft per month, by year’s end. Despite these latest issues, this reportedly remains the goal. Airbus is currently in the mid-40s per month, aiming for over 50 by the end of the year.
As we have seen, Airbus has had its own production headaches. The European manufacturer had to update or replace some of its oldest Finish Assembly Lines (FALs) for the A320 family. Airbus did much of this work during the pandemic, in the space it previously built the A380, in Toulouse, France. Airbus also wants to introduce another A320 production line in its US facility, in Mobile, Alabama.