Safran has been working on its Open Rotor engine design for some years. But what is it? And what advantages does it hold? Will it become operational?
It is certainly an unusual look. But at its heart, Safran’s Open Rotor is not a new idea. Previous iterations, from other companies had different names. ‘Unducted Fan (UDF)’ is one, ‘Propfan’ is another. In all cases, the concept was similar: a jet engine with large diameter fan blades, without the constraints of a cowling. Work on the idea began already in the 1980s, a few years after turbofans started to replace turbojets. To explain why, we need to see what a ‘bypass ratio’ is.
In very simple terms, a turbofan is a turbojet that has a bigger fan in front of it, with some airflow from this fan going around the engine itself (the core) and through, to the rear. Hence the term ‘bypass’: some air bypasses the engine core. Actually, A LOT of air. In the newer turbofans we see today, the bypass ratio can be 11:1. This means that for every one unit of air going through the core, we have eleven that go around it. And this bypassing airflow generates the bulk of the engine’s thrust.
Generally speaking, the higher the bypass ratio, the more efficient the engine. However, there are some practical limitations, about how big the bypass ratio of a turbofan can be. The bigger the fan, the bigger its cowling, containment ring and other structures will be. So it will be heavier. Also, it will require the wing to sit higher off the ground. Therefore it will require taller landing gear, or a different configuration of wing.
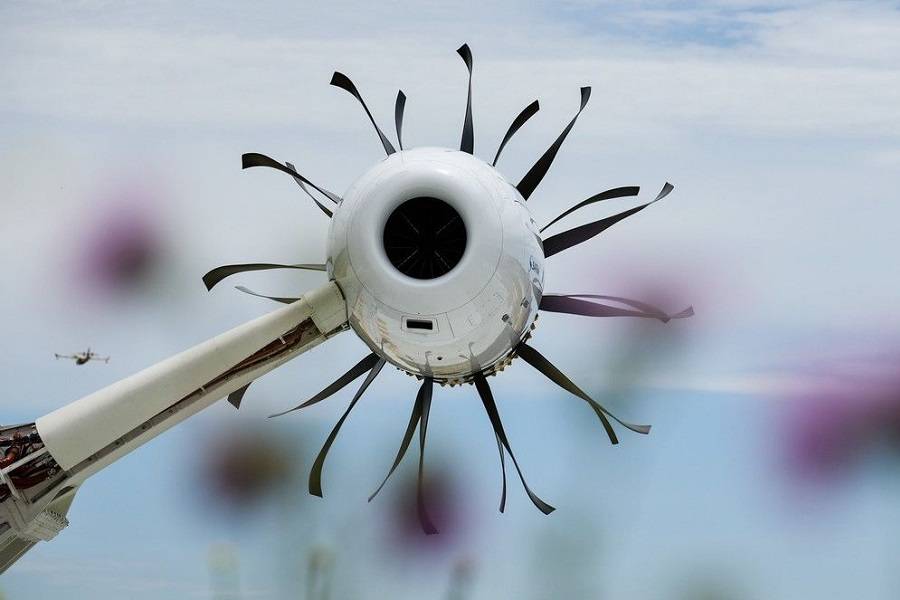
Safran’s Open Rotor: More Complicated, But Simpler!
Safran’s Open Rotor and other such designs get around these problems by exposing the blades. This allows much higher but still practical bypass ratios, around 30:1! Also, the structure is lighter than high bypass turbofans. This means that it is suitable for mounting near the tail of the aircraft. And the design makes for easier and simpler thrust reversing systems – if the blades have a variable pitch. And those in Safran’s Open Rotor, do.
One potential problem with these designs is noise. In a normal turbofan, the cowling helps keep the noise levels under control. The exposed tips of the blades would be much noisier. This was something engineers saw in earlier attempts with such designs. To get around the problem, engineers need to make the fan blades spin slower. In the Open Rotor, Safran is using a reduction gearbox. They also have a special design for the tips of the blades themselves, that greatly reduces noise.
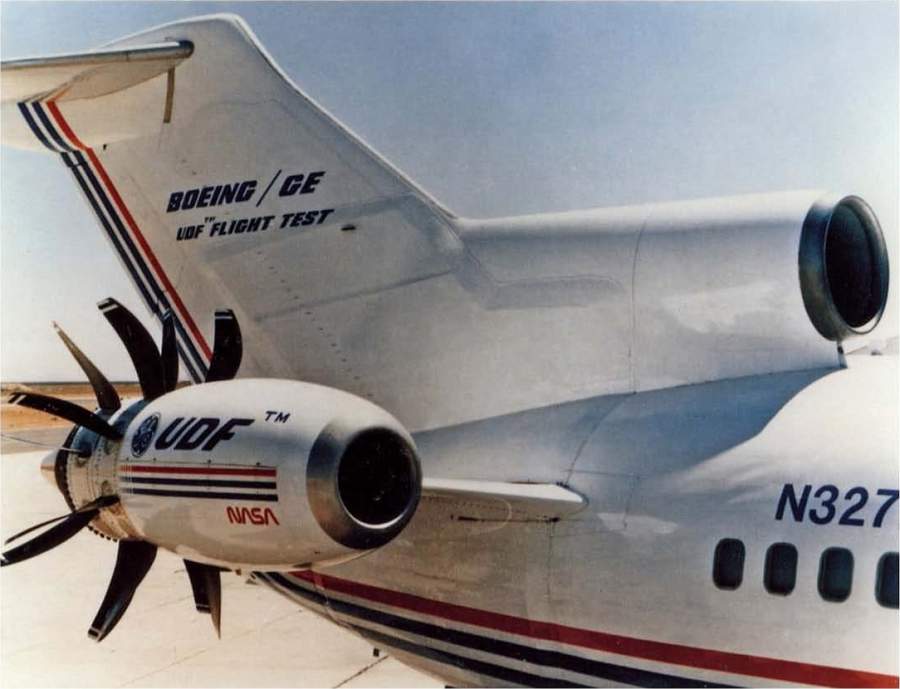
However in earlier designs there was no gearbox for the exposed fans. One notable such early design was the GE36 UDF. Safran (then called ‘Snecma’) participated in that program. This engine had the core of a military GE engine, the F404. And instead of a gearbox for the exposed blades, there was a shaft from each fan to an internal ‘free turbine’.
Free Turbine Versus Gearbox
This turbine sat in the exhaust airflow. And it had a configuration that gave it lower RPM. It is a simpler system than what Safran are doing with their Open Rotor. But it is not as efficient. Back then, reduction gearboxes had not yet proven their reliability. So airlines and aircraft manufacturers preferred to avoid them. This has changed now. And with the gear box, the speed of the blades is even lower than would be possible in the GE36.
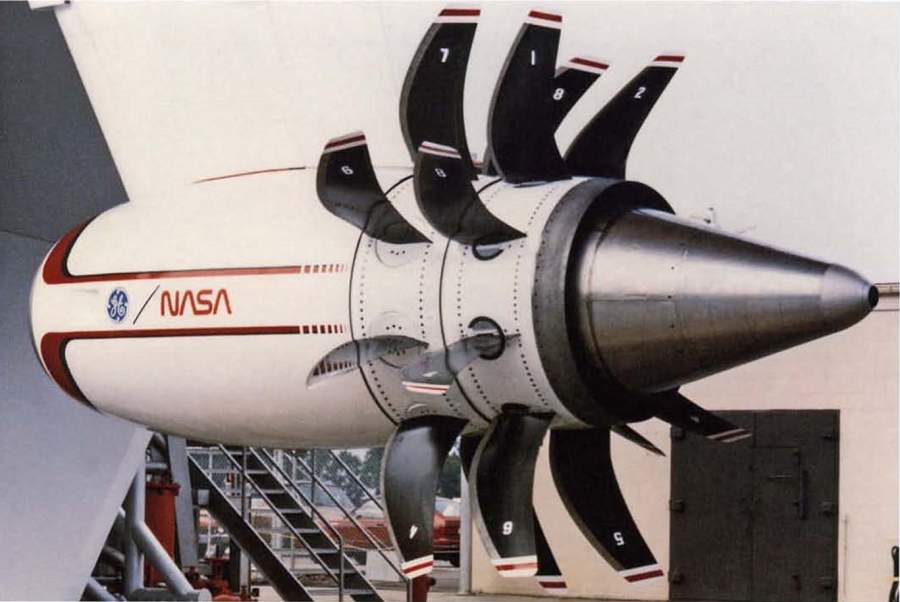
Combined with the ‘quieter’ blade tips, Safran claims that the Open Rotor is as quiet as a modern CFM LEAP-1 engine. The Open Rotor also has the core of a military engine, this time Safran’s M88. This is the engine that powers the Dassault Rafale. Interestingly, the first prototype of this plane had GE’s F404 engines instead! In the GE36 engine, the F404 engine installation still had its (small) bypass section. We don’t know if this is true of the M88, which is also a turbofan. Fighter jet turbofans generally have much lower bypass ratios, more suitable for supersonic flight.
So Safran’s Open Rotor doesn’t have the noise problems of older such designs. And with even higher efficiency thanks to its reduction gearbox, it promises 15% better efficiency than the CFM LEAP-1 engine. Remember, the LEAP is about that much more efficient than the CFM56! Another 15% better than that, is a leap ahead in efficiency. But there are some limitations here.
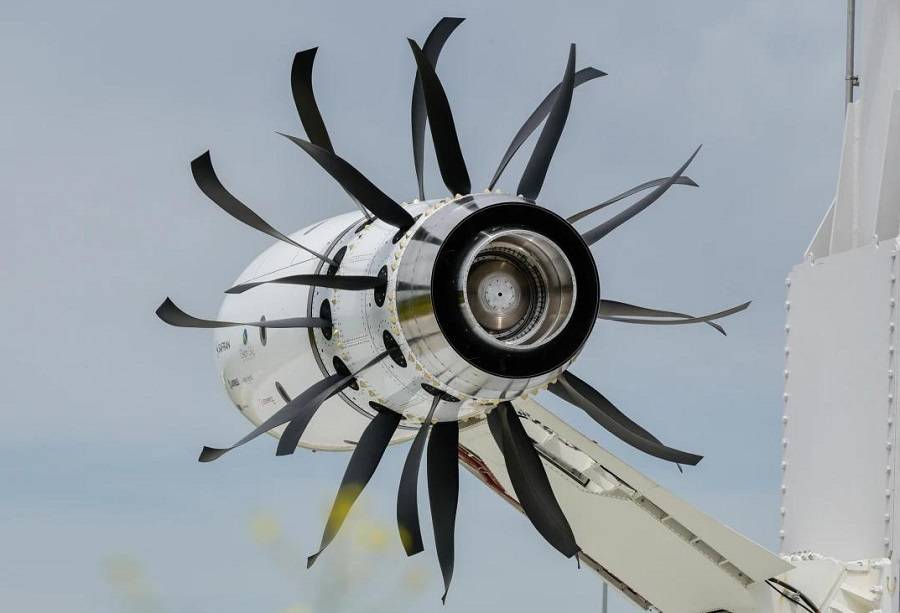
Open Rotor: Size and Safran’s Timeline
Safran’s test engine for the Open Rotor project, first ran in 2017. It has a fan diameter of four meters (nearly 15 feet). This means it probably won’t fit easily under the wings of many aircraft. Safran can actually reconfigure it, to have the fans in the front, instead. That could help with fit, under some wings. But realistically, the engine calls for a new aircraft design. And of course this takes time.
Also, Safran thinks that a production version of this engine will have to wait until around 2030. This is largely because of the need to figure out how to certify something like it. The Open Rotor needs to prove that it is as safe as Safran’s and others’ engines out there. The blade design has to prove that it isn’t susceptible to breakages, for instance. Thankfully, there is know-how from turboprop engine design, that should help in this regard.
Despite the obstacles and the timeline, everyone wants to reap the benefits of this technology. So if Safran can really keep it quiet, seeing Open Rotor engines in the sky, in a plane with passengers, may well happen! What do you think? Would you like to fly in a plane with such engines?
All pictures from Safran
7 comments
Carl Sciuk
Carbon fiber fan blades do not suffer the failures that require containment. Blade failures are generally from micro metal crystal anomalies that spread. So certainly can see the question of containment being a non issue.
Spyros Georgilidakis
Even if you hit a bird?
Bruce Atkinson
How much blood are the developers willing to spill when a blade severs the tail off the airplane? There are STILL uncontained fan failures in current engines that periodically don’t turn out well.
Andre T
Note there is an error in the article. It states “However in earlier designs there was no gearbox for the exposed fans.” but in the 80’s Pratt & Whitney/Allison 578-DX was geared and supposedly 7% better economy than the GE34. I have seen one of the remaining Pratt & Whitney/Allison 578-DX in museum at Pratt Whitney campus in East Hartford, CT.
https://en.wikipedia.org/wiki/Pratt_%26_Whitney/Allison_578-DX
Andre T
Comparison was made to LEAP which make sense being this is engine they are partnered to GE. The article talks to reduction gearing to achieve noise and other aerodynamic advantages to achieve greater bypass. The efficiency is compared to LEAP. But when reduction gearing was mentioned I thought of the geared turbojet. PW1000 approach to 15%+ efficiency was the geared fan and less stages than LEAP where the stages are where the got the efficiency improvement. The next level of efficiency of turbofan is combining the methods. CFM/GE knows this and why GE is challenging PW’ patent. This Safran project I believe is means to challenge the patent.
I believe the safety aspect propeller failure would be a challenge. Plane design would need to minimize high energy liberation of a blade. Plus diced will be quieter. Again geared turbofan is more quiet.
Alan Burton
The larger the fan blades the greater area exposed to potential damage such as bird strikes. I imagine being unducted also increases this risk since a sideways impact would be an issue whereas ducted would offer some protection. Material thrown up from ground effect maybe also needs consideration during t/o and landing ?
Ronald Wabwire
Looks very nice, o
I would love to fly on such an air plane. As stated, new form factor would for air plane would have to be created. I think the new blended wing would be suitable.