An article by Dale J Ferrier that explores the rich history and development of automatic landing aircraft systems. This is the second and last part in the series.
For Part One, click HERE.
Going Hands-Free
If further progress was to be made, it became apparent that it would be much easier if the two RAE/TRE teams working on the project did so from the same site. In this premise, a new unit was formed combining the teams into one at Martlesham Heath, East Anglia and was called the Blind Landing Experimental Unit (BLEU). By November 1945 work was completed in installing radio altimeters and autopilot couplings into the test aircraft, and the ILS (SCS 51) on the airfield itself.
Four overlapping radio beams marked out the glideslope and were displayed by an aircraft’s instruments, along with radio beacons marking set distances from the runway, so that the pilot could see his position relative to the runway regardless of visibility. If this could be connected to the autopilot, the aircraft could very well fly itself to the runway. Before that stage, however, there were some issues to overcome.
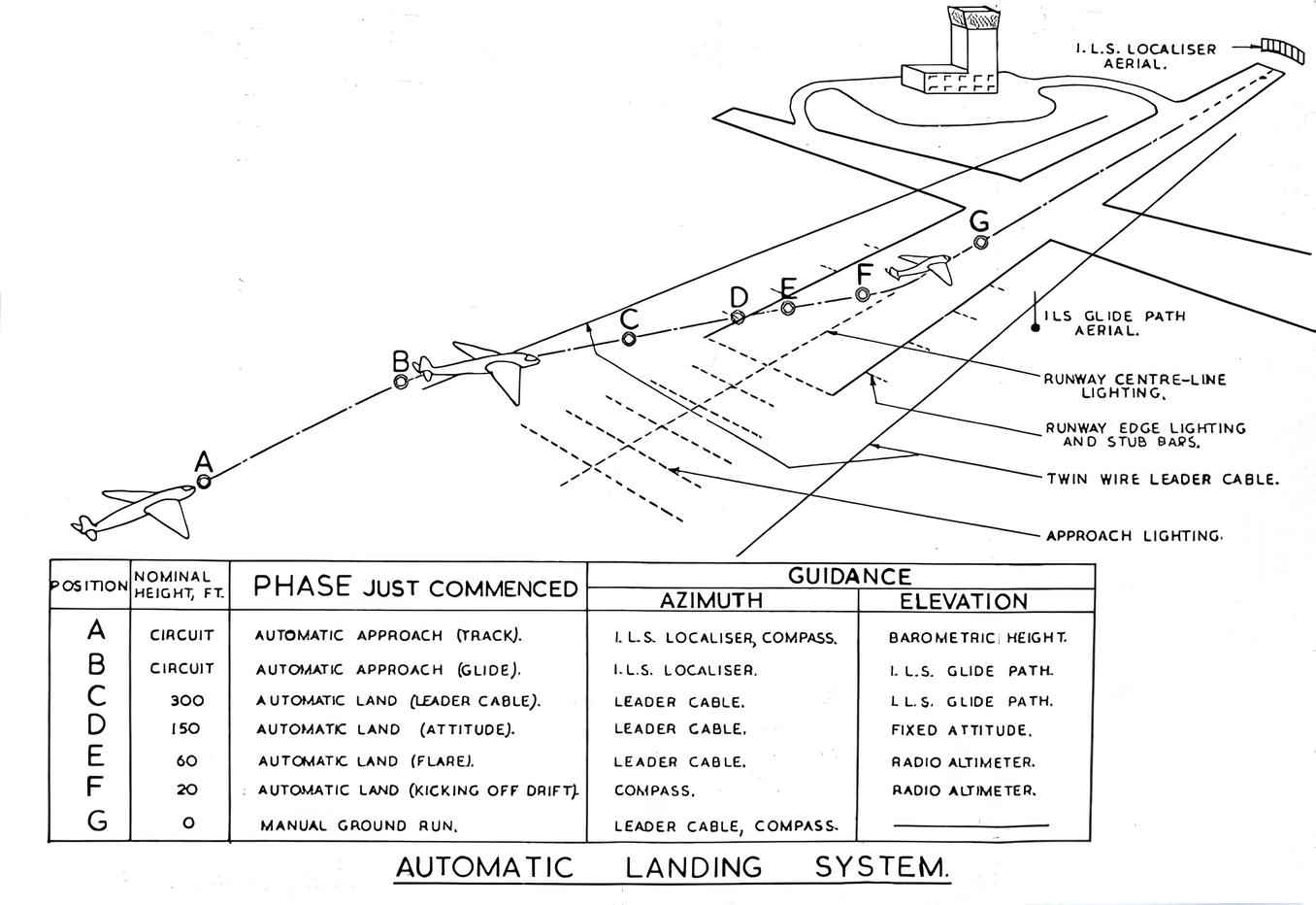
The ILS seemed to lose much of its accuracy below 200ft due to the radio beams being reflected off and disrupted by nearby buildings. BLEU’s task was to couple the ILS to the autopilot but make sure that it could be disengaged at any point in the event of errors, such as at low level when accuracy is lost. As for the last few hundred feet of an approach, the pilot would be required to fly manually. But in poor conditions, the pilot may not be able to see the runway clearly.
Whilst work was being done at BLEU, civilian airports were beginning to install approach lighting to assist pilots landing in the dark or poor conditions, but during these early years, there was no standard for these lights, so variation could be disorientating to pilots just emerging over them out of clouds. The RAE’s electrical department showed serious shortcomings in many of the proposed designs. Therefore, seeking to standardise runway lighting, they designed the 900m Calvert Centre Line and Crossbar design which was named after one of the project researchers. In 1949, through the new ICAO, it was adopted as the international standard and remains so today.
Quite often the reason a pilot would use ILS would be due to fog and so work was made to find out the worst-case scenario between Runway Visual Range and Slant Visual Range (how far can the pilot see down the glideslope) for which a pilot disengaging from the ILS could safely perform a successful landing. 800m RVR with a 200ft decision height was landed on and this became the basis for a Category 1 approach.
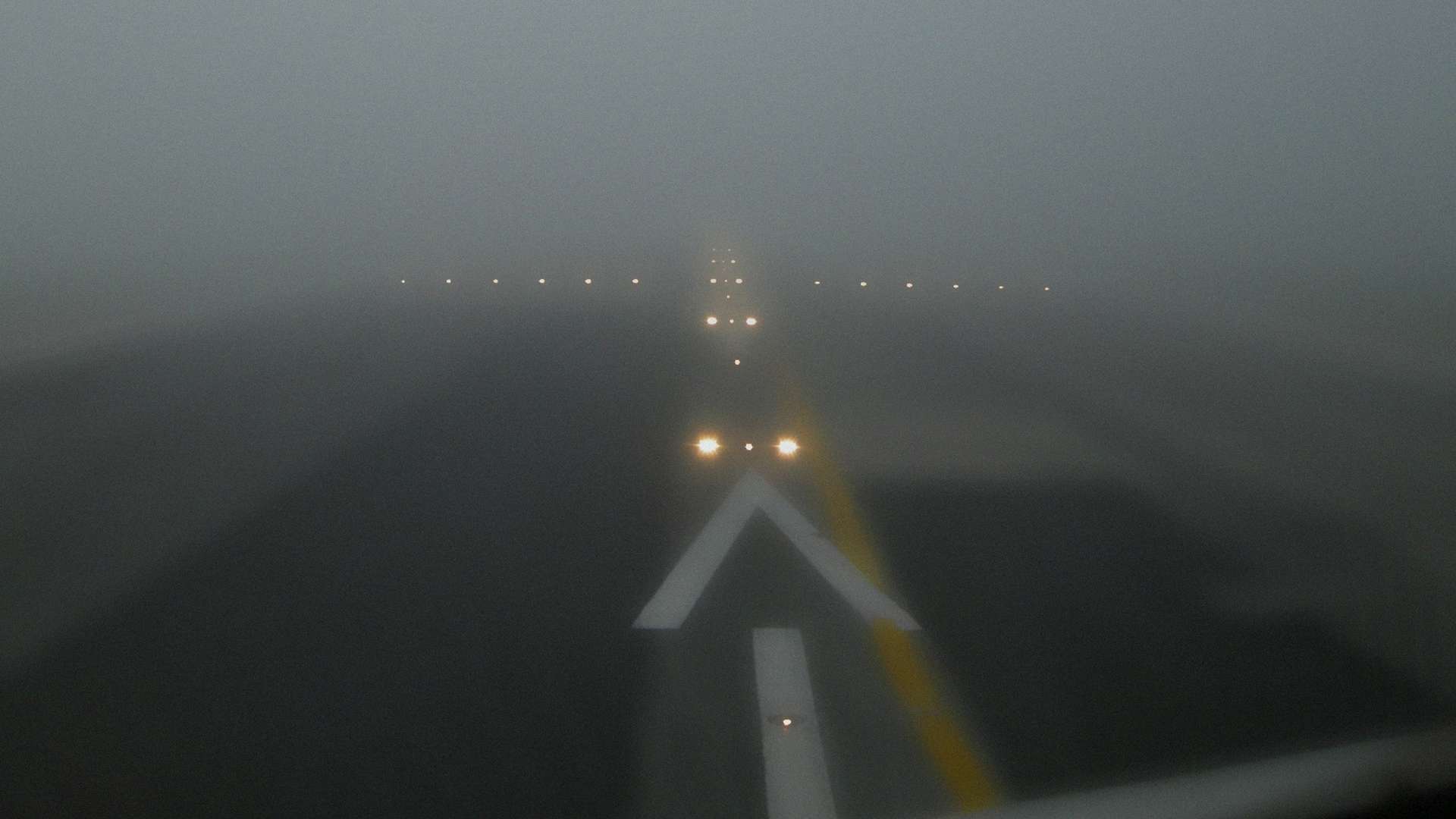
Although a Cat 1 approach may cover most landings in adverse conditions, the team at BLEU still remained convinced that a fully automated landing right to touchdown would be the safer option. Alternatives to full automation were considered, especially in the US where engineers remained uncertain over this very new technology being used at such a critical stage of flight. For example, in 1961, whilst the BLEU team continued apace with developing their fully automated system, the FAA was developing its own idea which kept the pilot in the loop. Small radio beacons were to be placed down each side of the runway which meant that its outline could be displayed on a CRT screen in the cockpit whilst the pilot remained in full command of their aircraft.
Although BLEU had already invested a great deal into the automatic solution, they had also looked into the same idea as the FAA but soon deduced that such a system would place a much greater workload on the pilot, and the system would be limited in the information it could provide. We can foresee that such a display would have been unlikely to provide the depth perception a pilot has during a visual landing and so give a false impression of the aircraft’s position, along with the potential disorientation the pilot may experience when transitioning from the CRT screen to looking out of the windshield. Other ideas were also being investigated, including the use of a HUD.
The inaccuracy of the ILS beams at low level remained a thorn in the side of BLEU which proposed overcoming this by breaking down the autoland process into 3 stages. Coordinating the ILS, the Autopilot, and the Autothrottle, the system would guide the aircraft down the glideslope until about 200ft above the ground. At this point, the system will ‘let go’ of the ILS beam and simply maintain the aircraft’s attitude and airspeed. Next, when reaching 70ft, the Autothrottle will begin gradually reducing power whilst the Autopilot begins the flare and removes any crosswind correction just before touchdown. Just when the flare would begin was fine-tuned for each aircraft type.
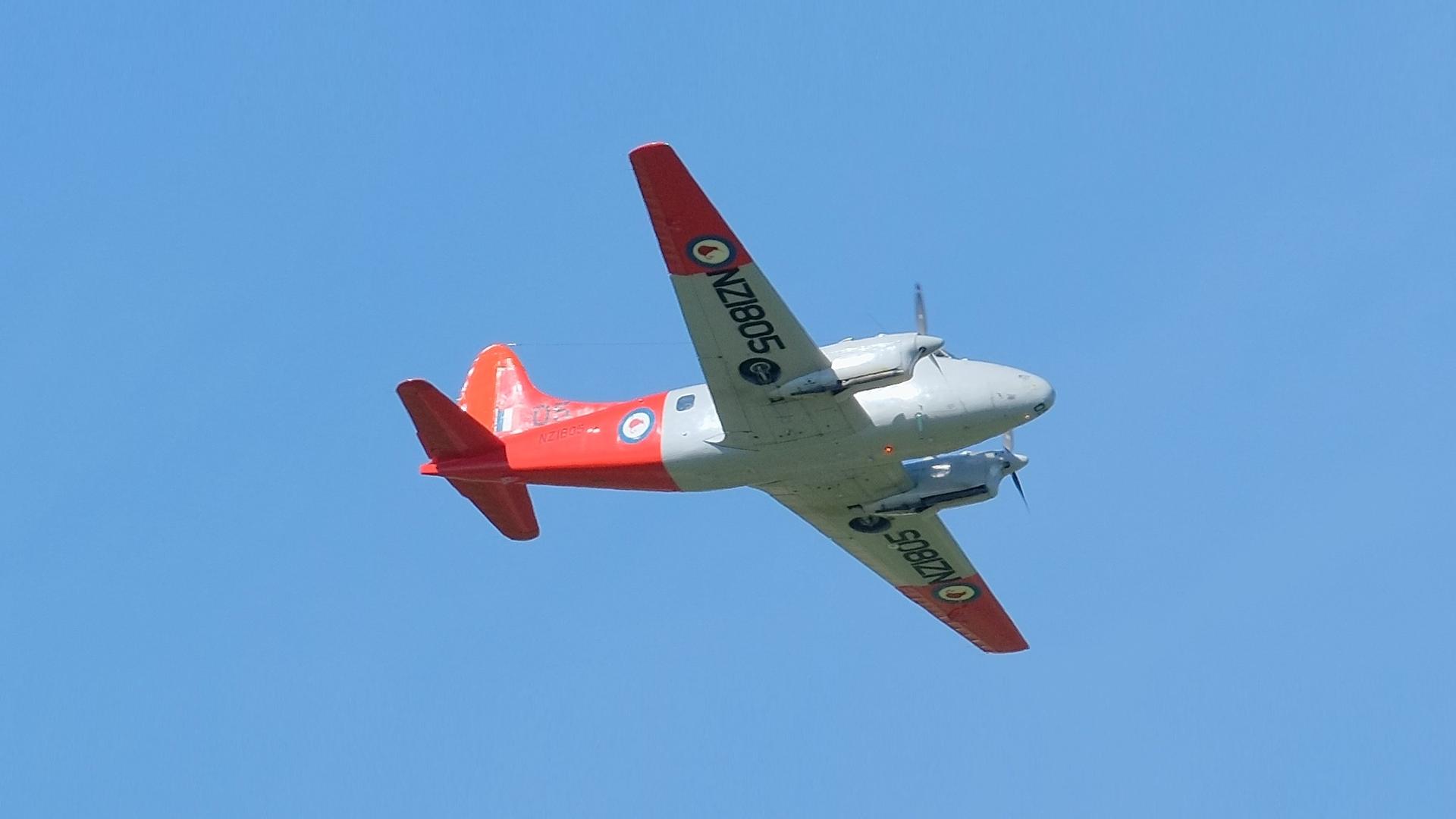
This system was installed and demonstrated on a DeHavilland Devon in 1950, with installations made on other airframes soon after. Although BLEU’s 3-stage autoland seemed to work in most situations, that didn’t prevent the occasional mishap such as when another RAE research aeroplane, an Avro Anson, made a hard landing collapsing the gear and skidded along the runway on its belly. Despite this, work progressed apace with the BLEU team moving onto ever larger airframes with a lineup including Vickers Varsitys, Canberras, and eventually a couple of Comets – the latter representing a more operational use. The success of the development was such that in 1954 a formal request was made to develop an autoland system for the RAF’s Vulcan bombers.
In 1957, BLEU was moved to the RAE airfield at Bedford which proved unpopular among the staff who had come accustomed to the leisurely sideside life with its fishing and sailing at the weekend. Bedford, however, was more suited for continuing development with its 300ft wide 2-mile long runway which saw little traffic, and by October 1958, BLEU felt confident enough to demonstrate their Autoland system to the Air Staff, CAA, airlines, industrial figures, and the press which had the pleasure of experiencing test pilot Pinkie Stark’s “look, no hands!” show. The spectacle of aircraft landing by themselves even attracted the attention of royalty. HRH Prince Philip, who had a long interest in pushing boundaries, paid a visit to BLEU and had a ride in one of the Canberras to see it for himself on December 4th 1959, and is said to have been greatly satisfied.
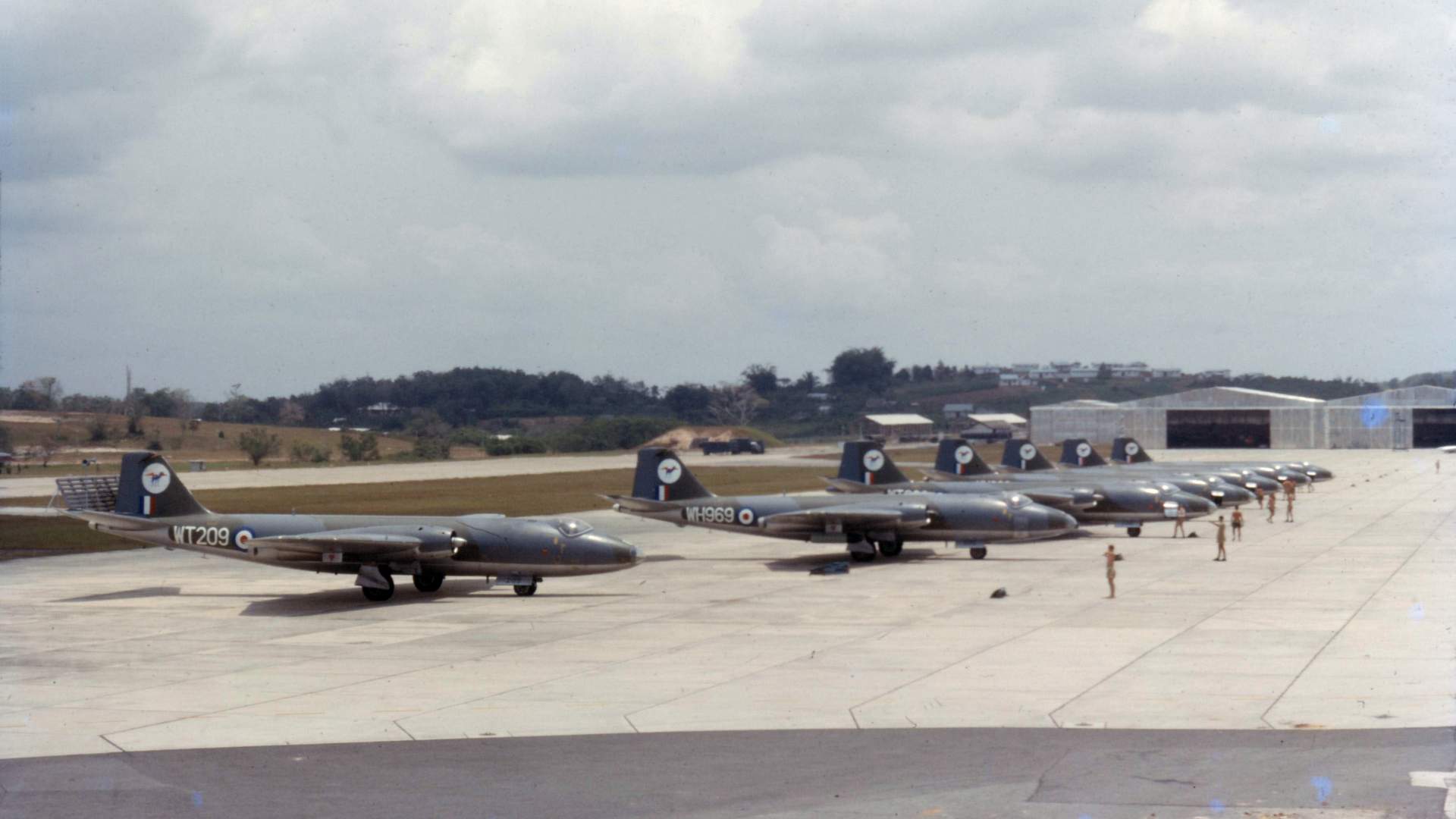
Going Public
So far BLEU’s Autoland system used a ‘Single Lane’ design which was fine on military aircraft, but with the potential for a single point failure, this design would not be acceptable for the civilian market. For Autoland to be used commercially, a multi-lane system would need to be developed so that should the primary lane fail, the system could fall back onto one of the backups. However, addressing the redundancy issue added greater complexity and cost as it would be essentially multiplying the system. But despite this, by now both BEA and BOAC had developed a keen interest in the project seeing the value such a system could bring to their operations. Working with the two carriers, the Air Registration Board, and industry leaders, BLEU went to work to ready their Autoland for introduction to the commercial market.
Early on it was known that certifying their autoland for use right to touchdown would likely take an unfeasibly long time, which airlines would be unwilling to wait for. To address this and ensure the airlines backing BLEU got to use it in a realistic time frame, a stepped approach to certification was proposed. As the system became progressively more accurate over the years, a set of gateways or checkpoints could be implemented which would allow Autoland to be used with certification updates taking place as time went on.
This was proposed and accepted by ICAO which, based on minimum decision heights, rolled out these gateways across its member states. Each gateway, or category of automatic landing, equated to a lower height for which the pilot must be in sight of the runway. The categories were; 1, 2, 3A, 3B, and 3C. These remain the case today with the various aircraft and airports being certified upto a category that they have the equipment for. Many smaller regional airports may only be certified for Cat 1 or 2, whereas major hubs will likely have Cat 3C.
Category | Decision Height | RVR |
Cat I | 200ft | >550m |
Cat II | 100 – 200ft | >350m |
Cat IIIA | <100ft | >200m |
Cat IIIB | <50ft | >50m |
Cat IIIC | None | None |
The FAA remained unsure of BLEU’s design and was still pursuing the idea of keeping the pilot in the loop rather than handing control entirely to the autopilot. To assess the feasibility of the Autoland system, they sent a Douglas DC-7 to Bedford to be fitted out and trial this system over 3 months. These trials convinced the FAA of the functionality and safety of BLEU’s fully automated design and the DC-7 returned to Atlantic City having fulfilled its duty. However, as mentioned earlier, the FAA continued to work on their alternative ‘in the loop’ idea for some time afterwards.
Although the Americans were seemingly convinced, the impetus to implement automatic landings was stronger in Europe with its more frequent low visibility conditions. In 1959 contracts were signed with Smiths Industries to supply a Triplex Autoland on BEA’s new upcoming Hawker-Siddeley HS121 Tridents, and with Elliots to supply a Duplex Autoland for BOAC’s Vickers VC10s, although this was later cancelled.
Smiths’ Triplex Autoland used a kind of voting system which would detect and disconnect a failed lane, falling back onto one of the others to complete the operation safely. Their triple-lane Autoland wasn’t the only innovation made by Smiths whose certification process and statistical analysis laid the foundations for how avionics were developed going forward.
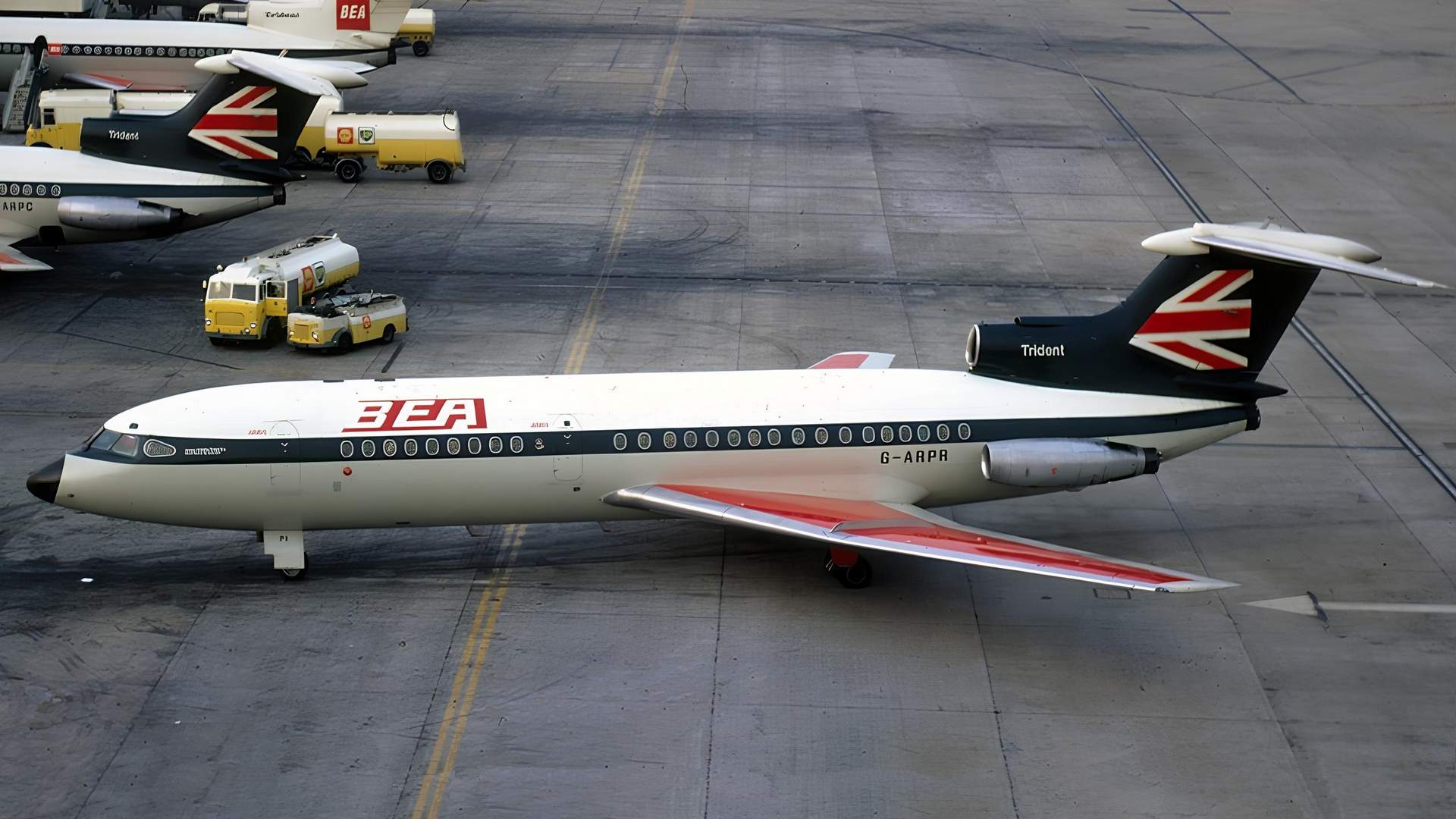
The Triplex Autoland was fitted to BEA’s Tridents and on October 6th 1965, a Trident 1C (G-ARPR) flew from Paris Le Bourget to London Heathrow as flight BE343 and performed the world’s first Autoland on a scheduled passenger service. BEA’s use of Autoland dramatically improved the airline’s on-time performance and dispatch reliability during the winter, much to the delight of its bosses, even if pilots of these first flights were somewhat anxious about letting go of the controls so close to the ground.
But, early inaccuracies meant that from time to time, these early Tridents made hard landings and during inspections in the 1970s, fatigue cracks were found in some of their wing spars. Rather than perform the costly repairs, BEA elected to simply withdraw and scrap the affected Tridents. But, despite causing the eventual demise of some early aircraft, Autoland proved itself a great asset for operators and soon its use grew into a much more regular occurrence.
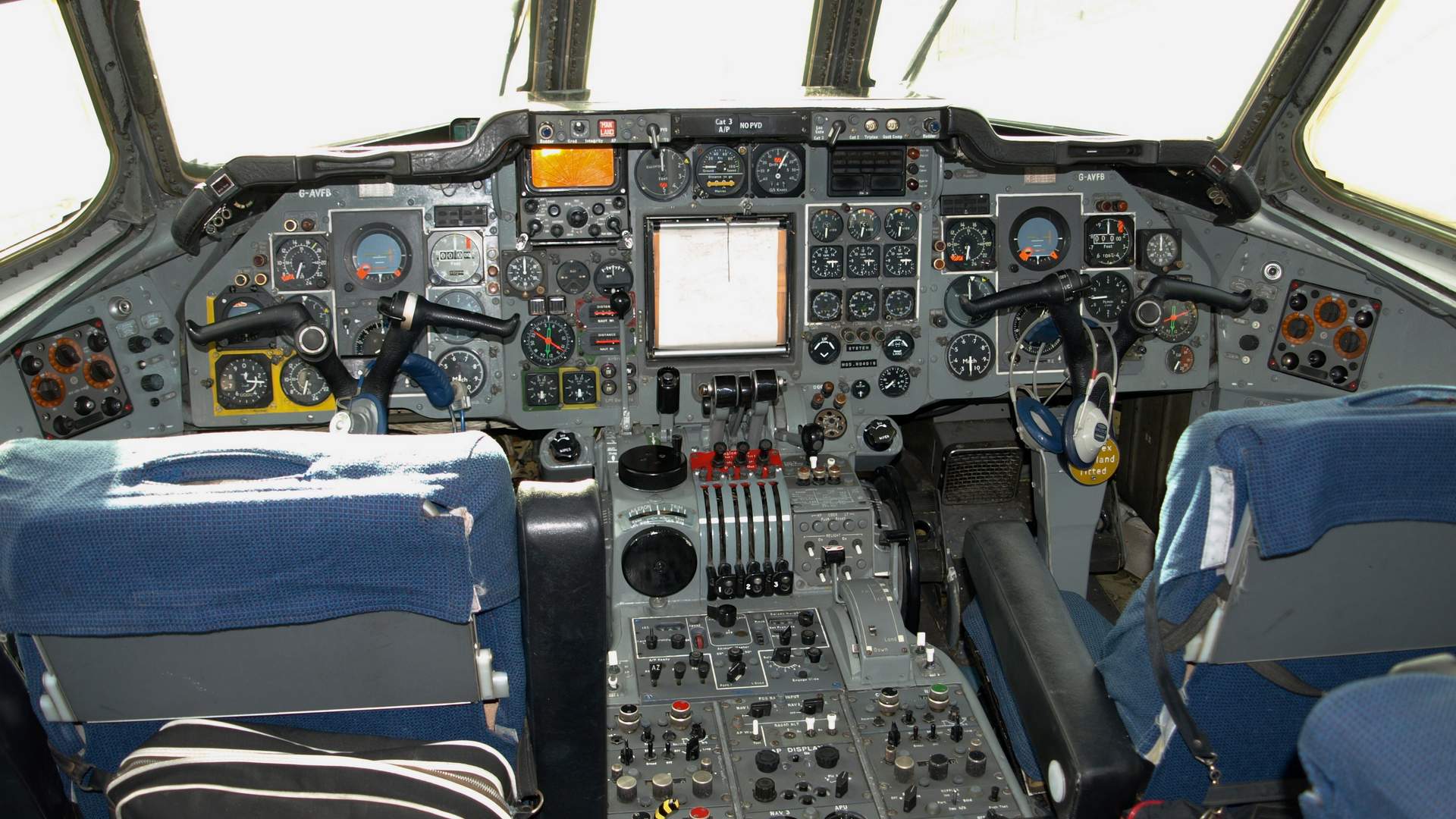
Progress to improve the system’s accuracy and thus certified category progressed with statistical analysis carried out over many thousands of landing cycles not just in Tridents, but also BAC1-11s, VC10s, and even Concorde. This meant that in 1979, Tridents were certified for Cat 3C landings meaning they could land in zero visibility. Interestingly, early Boeing 757s were fitted with Cat 3B certified Autolands only meaning that for a time, an older 1960s-designed aircraft was allowed to fly into poorer visibility conditions than Boeing’s new cutting-edge airliner of the 1980s.
Other avionic manufacturers were developing their own Autoland systems with Sperry installing theirs in Pan Am 727s, and Collins’s innovative version in BA’s Lockheed L1011 Tristars. Collins developed a much more integrated design and rather than use attitude hold for the last stages of the approach, it used inertia-derived data to provide much more accurate control to the ground.
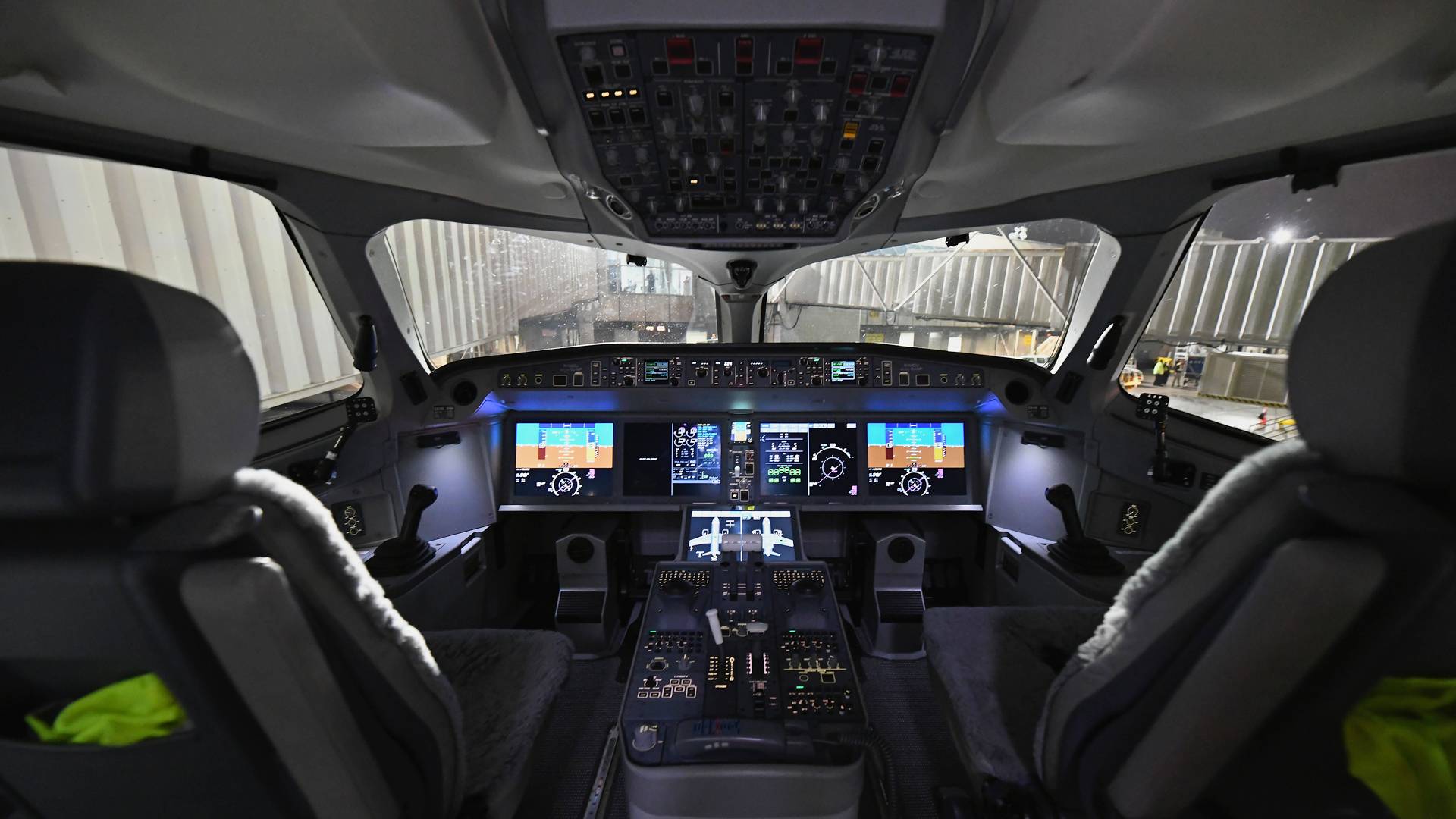
Just Another Day in the Office
Today, using Autoland is a routine and mundane procedure for airline pilots. But, for those early pioneers, taking their hands off the controls and letting the electronic wonders in front of them takeover, all the whilst not being able to see where they were heading, must have been a somewhat unnerving experience at first.
Today, further innovations using GPS-based Autolands allow operators to land at airports without the necessary ILS infrastructure, and the development of an emergency Autoland for general aviation shows that the story of this remarkable system isn’t over. The work of BLEU and that of those who developed ILS has meant that airlines and passengers alike can take to the skies in much greater confidence that a bit of low cloud or fog will be unlikely to scupper their plans – a luxury not enjoyed by early aviators. What wonders lay behind the APP button.
References
- Journal of Aeronautical History, Vol 1, Paper No. 2011/1, The RAE Contribution to All-Weather Landing, by Sir John Charnley CB MEng. FREng. FRIN FRAeS
- Airways Magazine, 6/10/1965: World’s First Automatic Landing, by Lee Cross, June 10th 2023
- Smithsonian Magazine, The First Autolanding, by George C Larson, August 2012
- Farnborough Air Sciences Trust (FAST), The Royal Aircraft Establishment at Bedford, The Blind Landing Experimental Unit (BLEU)