Drawings and scale prototypes of blended wing body designs have been around for some time. But why don’t we have one in production yet? What are the challenges of making these designs work?
As we discussed recently, there aren’t many developments in aviation that lead to leaps in efficiency. Not that they don’t happen. We actually had such an example very recently. The new-generation engines in 737s and A320s gave double-digit efficiency gains in fuel consumption. And simple things like ADS-B and other satellite-driven navigation tools, make trips shorter and more efficient, too.
Now many believe that blended wing body designs could be the next technological leap in efficiency. The problem is, the idea has been around for a while, but doesn’t seem to ‘stick’. With the exception of the Northrop B-2 bomber, that is. But that’s really a flying wing, not a blended wing body. It has space for fuel and bombs, but not dozens or hundreds of people.
Before we study blended wing body designs, perhaps we need to look at the alternative. We need to study why ‘normal’ planes look like a tube with wings. The quick answer is, they’ve been made like this for a while, and the design offers many simple advantages. Sections of fuselage can be added or removed, to vary the design. The tubular shape has a small frontal area, that is simple to handle aerodynamically.
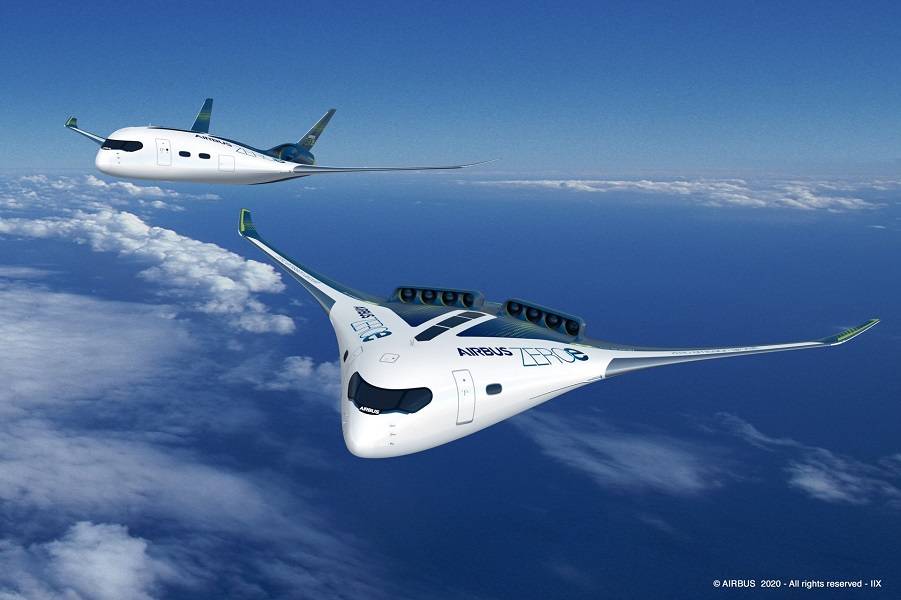
Moreover, the tubular shape means having a consistent and predictable internal layout of seats. And very importantly, it’s a design that offers the possibility of a large number of doors. This helps immensely, when designing emergency evacuation procedures. This is something that some blended wing body designs may struggle with.
Efficiency Gains?
So then, what advantages would blended wing body designs have? The answer is primarily efficiency. Having the entire fuselage as a lifting device, means a very low wing loading. It also means it will be possible to make the wing itself smaller, and still achieve slow-enough take-off and landing speeds. This reduces drag considerably. And in 2017 NASA invited aerospace manufacturers to come up with designs that would realistically be possible to implement by 2035. And reduce fuel consumption by 60-80%.
To put that number in perspective, Boeing’s goal for the efficiency of the 737 MAX, was to improve on the 737 NG by 14%. Airbus achieved similar gains with its A320neo, as well. Of course the two makers achieved this mainly with new engines – and winglets, and in Boeing’s case, a more ‘slippery’ tail-cone. A new fuselage making use of lightweight composites would be better. A sleek, laminar flow wing? Even more. But 60-80% better? Erm… no.
Not all the designs that aerospace manufacturers came up with, to meet NASA’s challenge, were blended wing body concepts. One was Boeing’s TTBW, that we have seen before. Another was the Double Bubble D8 – which definitely deserves its own article. But three other designs all revolved around the blended wing body idea, with small but interesting variations.
Boeing’s Blended Wing Body
Boeing and NASA have worked on a blended wing body research concept before. This was the X-48 program. It last flew in 2013. This was a scaled design, with two or three small turbojet engines. Boeing’s proposal, to meet NASA’s recent efficiency invitation, closely followed the latest iteration of that scaled design. This was the X-48C. It had two engines, mounted on an extension of the fuselage, and shrouded by two angled vertical stabilizers and rudders.
The placement of the engine reduces the noise footprint of this blended wing body considerably. This was a stated goal of NASA’s, as well. Today aircraft often have to modify their operations around urban centres, to minimize noise pollution, especially at night. This reduces efficiency. So in theory, a quieter aircraft would be able to operate more efficiently.
Among Boeing and NASA’s stated goals for the X-48 blended wing body program, was to demonstrate stable flight in both high and low speeds. This they did successfully. In earlier studies, Boeing and McDonnel-Douglas engineers reportedly solved another problem: evacuation. As stated above, this isn’t an issue with current jets. But it is a consideration for any would-be blended wing body jet, that would operate as a commercial airliner.
DZYNE Technologies
This is another take on the blended wing body that has a lot in common with Boeing’s. It actually looks a lot like the first iteration of the Boeing-NASA X-48B. That one had rudders at the ends of the wing, looking like oversize winglets. DZYNE is working on such a concept, for a large corporate jet or a regional airliner.
DZYNE believes that its blended wing body concept will be 35% more efficient than the best possible, all-composite ‘tube’-shaped airliner. They also think that its shape means that boarding and disembarkation will be faster. That’s because the distance from the entrance to any of the seats is only 10 rows away, rather than 25, for a large regional jet.
Not Quite Blended – Lockheed’s Hybrid Wing Body
This one is interesting, if only because it looks almost… conventional! The front half of the fuselage appears blended with the wing. But the rear half looks like that of a military cargo jet. It could even include a rear loading ramp! The T-tail is reasonably conventional. However the mounting of the engines is not. Generally, engineers avoid placing engines over the wing, for aerodynamic reasons.
Having the engines above and behind the wing, however, should work. In fact, the Honda HA-420 HondaJet has such a layout today. The problem with the layout is more structural. Having the weight of an engine resting on a long beam-like pylon behind the wing, would normally be difficult. But here, that section of the wing is perhaps thick and strong enough, to work! This design would probably see use in the military, rather than the airlines. Troops generally don’t complain about not having windows!
More Challenges
Certification of blended wing body designs is an unknown. Until someone tries it, we simple don’t know what challenges will arise. Proving evacuation in different emergency scenarios, in particular, is a question mark.
Airport infrastructure is another one. In theory, the use of the fuselage itself as a lifting surface, means that wings in blended wing body designs are much smaller. This could mean that aircraft of comparable passenger capacities would have comparable widths with existing designs. Again, this will be a question mark, until we see it in practice.
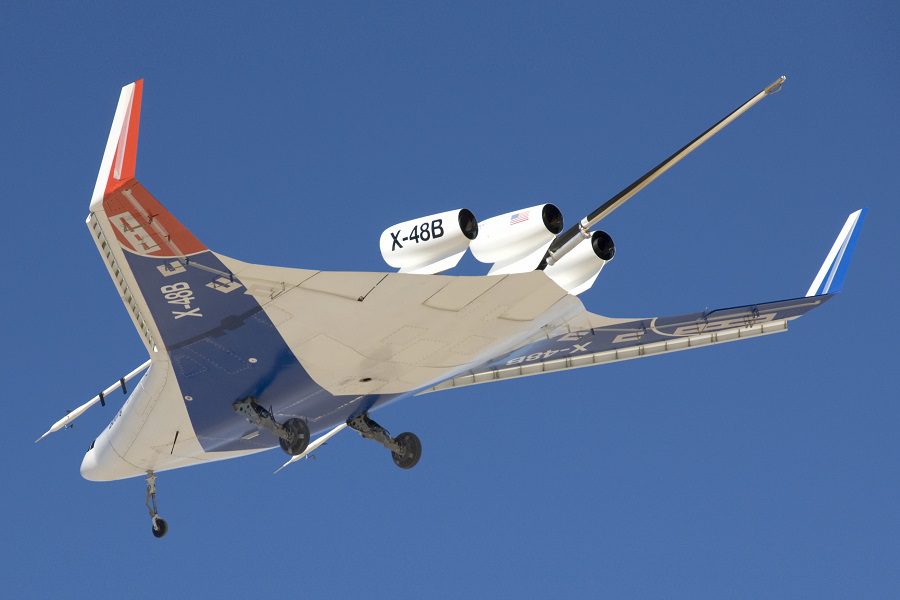
The one thing we know we have today that helps, is experience in structural composites. Keeping an aircraft pressurized when its shape is complex, is difficult. Composites are important, in making these shapes possible with a lightweight structure. That means that seeing blended wing body designs at airports, where we might board one, is more likely now, than ten years ago!
1 comment
Andre T
My question. Can these designs meet FAR 25.629 Aeroelastic stability requirements? B-2 wouldn’t. Flying wings are inherently aerodynamically unstable. Perhaps not issue with some blended designs.
Other challenges manufacturing cost and maintainability. Current aircraft design has evolved to better maintainability. For example the engines under wings gives maintainers great excess to make repairs at the gate if necessary. Airlines are not going to be happy having to roll aircraft into hanger to make a repair that used to be a 30 minute repair on conventional design.
Economics will win out. The other challenge.