In an age when efficiency is everything, the Airbus BLADE project showed how laminar flow could literally shape future airliners.
In Airbus parlance, BLADE stands for “Breakthrough Laminar Aircraft Demonstrator in Europe”. A bit of a stretch, terminologically speaking, but it gets the point across rather well. Laminar flow is about cutting the air like a blade, figuratively speaking, and Airbus hoped to do just that. But before we have a look at the test aircraft, let’s see what laminar flow is.
The term simply refers to how air behaves very close to the wing. Very early on in aviation, we learned that there is a boundary layer of air over the wing, that is usually turbulent. This turbulent layer creates drag. This drag increases with speed. The Airbus BLADE is a study in shaping and manufacturing a real-world wing section, that achieves laminar flow. In simple terms, we can think of ‘laminar’ to mean ‘smooth’. Laminar flow also applies to fluids.
In aviation, it is possible to achieve laminar/smooth flow with either ‘natural’ or ‘hybrid/induced’ methods. The Airbus BLADE is in the former category, whereby laminar flow happens thanks to the shape/smoothness of the wing. Other methods involve cutting microscopic holes in the upper surface of the wing. Then a pump draws air in through the holes, to get rid of the turbulent air, leaving only smooth/laminar flow. This works too, but adds weight and complexity.
Laminar Flow Testing Before The Airbus BLADE
Laminar flow tests in flight, are nothing new. The first such tests took place shortly before WWII! But unlike the Airbus BLADE, these laminar flow tests involved active/hybrid setups. They also involved structures placed on top of an existing wing. So the laminar flow surface was not structural to the wing. This was perfectly acceptable for those early tests, because the objective was to prove the technology.
One notable example of laminar flow testing that preceded the Airbus BLADE was NASA’s supersonic testing. This involved a modified version of the (already modified) F-16XL. But those tests were primarily about supersonic commercial aviation. This aircraft had an added structure on its left wing, with thousands or (in a later version) millions of tiny holes.
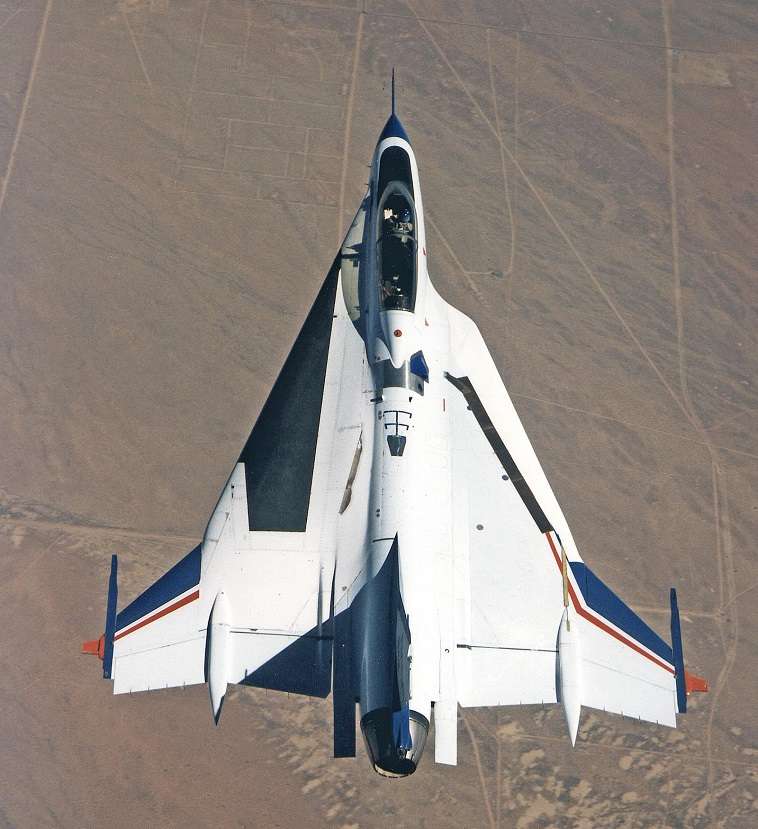
The aircraft sucked air through these small holes, using pump running on bleed-air from the engine. It worked well enough that this aircraft could accelerate supersonically without using afterburner. This boded well for then-future supersonic airliners, that wouldn’t use afterburners, either. Alas, the project didn’t find uses in civil/commercial aviation. However this could change soon.
But this is for supersonic travel. For most airliners, something simpler would be ideal. So Airbus wanted BLADE to show that natural laminar flow can work in practice, in a real aircraft. This meant making the laminar wing functional, with moving ailerons and, ideally, slats and spoilers as well. Airbus didn’t quite manage all of that. There are no slats in the front of the test wing sections, and obviously no spoilers, that far out into the wing. But each test section has an aileron.
The Test Aircraft
The BLADE laminar flow testbed is of course the Airbus A340-300. This is actually the very first prototype of that aircraft, and uses four CFM56 engines. Its outer wing sections now each sport a completely new wing structure, making use of composites. Pods on either side isolate them from the rest of the wing. And these pods also incorporate cameras and other flight test instrumentation (FTI).
The aircraft first flew in late 2017, beginning its test flight programme in early 2018. The wing profile has less sweep than the A330/A340 wing. That is because Airbus primarily wants BLADE to study laminar flow in short-haul, single-aisle aircraft. So, wing sweep for the BLADE airfoil is only 20°, whereas the rest of the wing is 30°. This makes it suitable to Mach 0.75, instead of the A330/A340’s more usual M0.82-0.84.
Airbus’ goal was for the BLADE sections to have laminar flow along 50% of the chord length (front-rear of the wing). Most wings achieve laminar flow only just behind the leading edge, before becoming turbulent. If the programme achieved this goal it would amount to an overall drag reduction of 8%. For a typical medium-haul 800nm flight, this means a fuel saving of 5%.
Airbus BLADE’s Laminar Flow Performance
At BLADE’s conclusion in April 2018, Airbus announced that its laminar flow results exceeded expectations. Not only was drag reduction lower by 10%, but the benefits were there at even higher speeds, of around Mach 0.78. Laminar flow remained stable even as the wing flexed in flight. Airbus had also taken the opportunity to test different materials on either side, for the leading edges. And they reported that both carbon composites and aluminium worked, with slight performance differences.
The technology is very promising, but there is a catch. Airbus has to determine how BLADE’s laminar flow changes with contamination: dirt and icing. We’ve already discussed how airlines are washing their aircraft, so they stay efficient. That’s all about airflow, and dirt, ice or even rain droplets can play a role.
Overall, Airbus declared BLADE to be a resounding success, with a lot of knowledge on laminar flow improving as a result. It is fair to say that the testing is not as impressive as NASA’s supersonic tests. But it could find use in airliners much sooner, and for more passengers.
After BLADE, Airbus reportedly wanted to see how laminar flow could work with morphing flaps and wings. This would eliminate separate parts, making for smoother surfaces. Unfortunately the pandemic put a halt on various research projects, including this one. But there is still time until Airbus or Boeing embark on a new single-aisle design!